COLUMN 特集記事
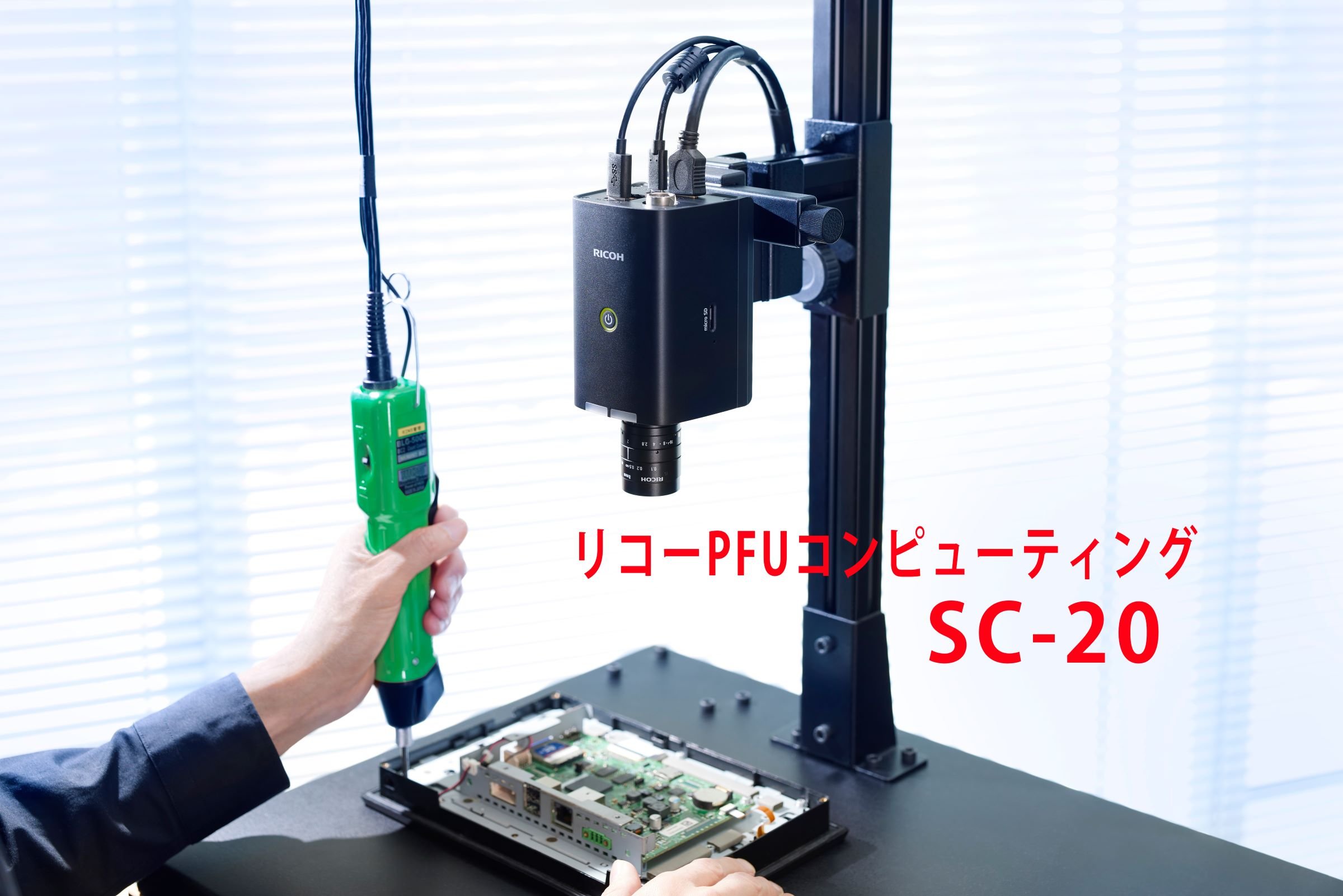
- 製品紹介
製品概要
リコーPFUコンピューティングの SC-20は、組立工程における作業ミスをリアルタイムで検出する作業検査カメラです。従来の目視検査では困難だった小型部品の取り付け状況や取り付け方向のチェック、質感マッチング判定による不織布やスポンジなどの有無検査が可能です。これにより、手作業工程の品質向上と不良低減、トレーサビリティチェックなど期待できます。また低価格でありつつ多機能であり、PCも不要なためトータルコストを抑えて導入できます。
こんなお困りはありませんか?
-
DX機器を導入したいけど設置できる人材がいない
→パソコン不要の簡単設置で誰でも簡単にセッティング可能。
-
チェック漏れが多発する
→リアルタイム検査でOK判定にならないと次工程に進まないのでチェック漏れが防げる。
-
作業者によって作業品質がばらついてしまう
→作業品質チェック機能を搭載。人による作業品質ばらつきを抑える。
-
作業効率があがらない
→作業時間の制限や品質管理を同時に行い作業効率を上げる。
-
トレーサビリティが確保できていない
→デジタルで蓄積データを管理しているので、後追いが可能。
-
高額な設備導入費用をかけられない
→制御にパソコンを使用しないため、トータル的にリーズナブルに導入が可能。
導入メリット
-
品質の均一化
目視検査のばらつきを抑制し、作業品質の均一化が図れます。 -
作業効率の向上
リアルタイムでの検査により、作業後の再検査の手間を削減できます。 -
トレーサビリティの確保
検査結果を画像ログとして保存し、作業分析やトレーサビリティに活用できます。
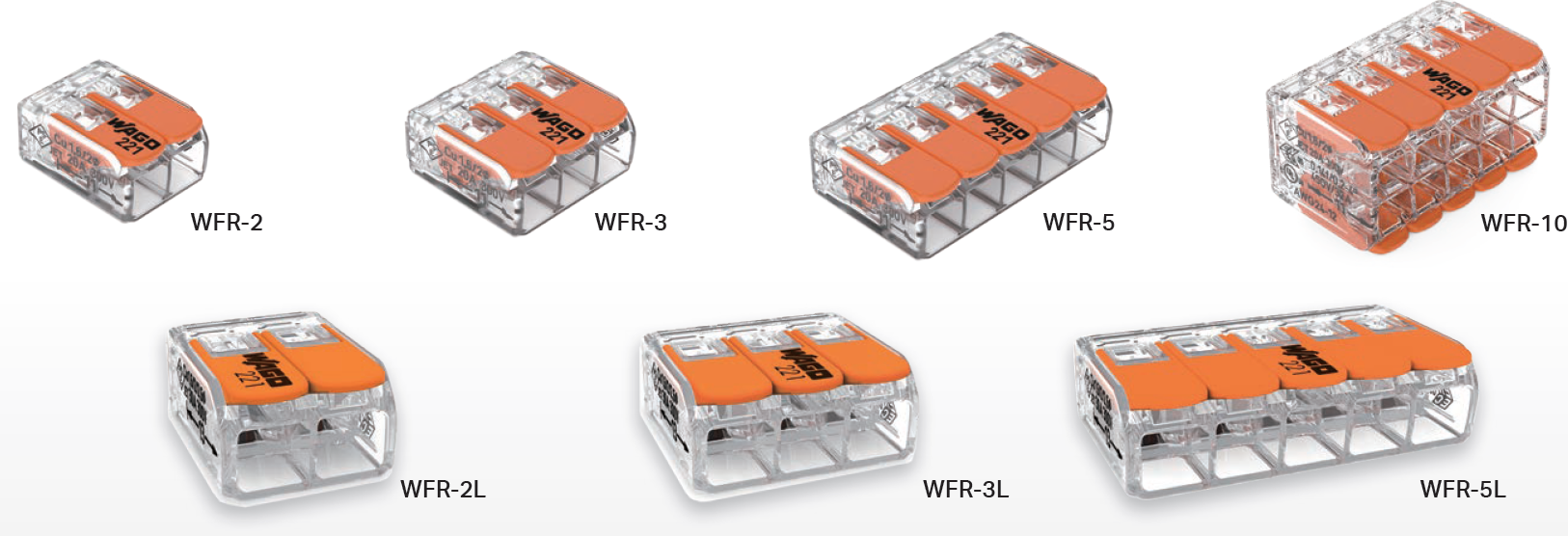
- 製品紹介
ワンタッチコネクタWFR/WFR-Lシリーズ
WAGOのワンタッチコネクタWFR/WFR-Lシリーズは、配線作業を簡単かつ安全に行うための革新的な製品です。
透明ハウジングやソフトなレバー操作など、多くの特長を持つこのシリーズは、屋内配線や一般電気工作物など、さまざまな用途に対応しています。
本記事では、WFR/WFR-Lシリーズの特長や使用方法、製品ラインナップについて詳しく紹介します。
WFR/WFR-Lシリーズの特長
-
透明ハウジング
WFR/WFR-Lシリーズの透明ハウジングは、結線状態を目視で確認できるため、安心して使用できます。これにより、結線ミスを防ぎ、安全性が向上します。 -
対応電線
このシリーズは、単線、IV7本より線、可とうより線の混在使用が可能です。幅広い電線に対応するため、さまざまな配線作業に適しています。 -
操作性
ソフトなレバー操作で簡単に結線できるため、作業効率が大幅に向上します。レバーを押し上げて電線を挿入し、押し下げるだけで結線が完了します。 -
用途
WFR/WFR-Lシリーズは、屋内配線や一般電気工作物など、さまざまな配線作業に使用可能です。内線規程や公共建築工事標準仕様書にも適合しており、信頼性の高い製品です。
結線方法
ステップバイステップガイド
- 電線の準備:ストリップゲージで電線の長さを確認し、正しい長さにむき出します。
- レバー操作:レバーを押し上げて電線挿入口を開きます。
- 電線の挿入:むき出した電線を突き当たるまで差し込みます。
- 結線完了:レバーを押し下げて結線を完了させます。
- 確認:電線を軽く引っ張り、抜けないことを確認します。
注意点
• 指を挟まないように注意する。
• 差し込みが不十分だと導通不良や発熱の恐れがあるため、正しい剥き長さでしっかりと差し込む。
メリット
WFR/WFR-Lシリーズを使用することで得られるメリットを以下にまとめます。
- 安全性の向上:透明ハウジングにより、結線状態を目視で確認できるため、結線ミスを防ぎます。
- 作業効率の向上:規定の長さに電線をむいてレバー操作するだけで、簡単に結線できるため、作業時間を短縮できます。
- 多用途対応:単線、IV7本より線、可とうより線の混在使用が可能で、さまざまな配線作業に対応します。
- 信頼性:内線規程や公共建築工事標準仕様書に記載があるため、信頼性の高い配線が求められる場所でも安心して使用できます。
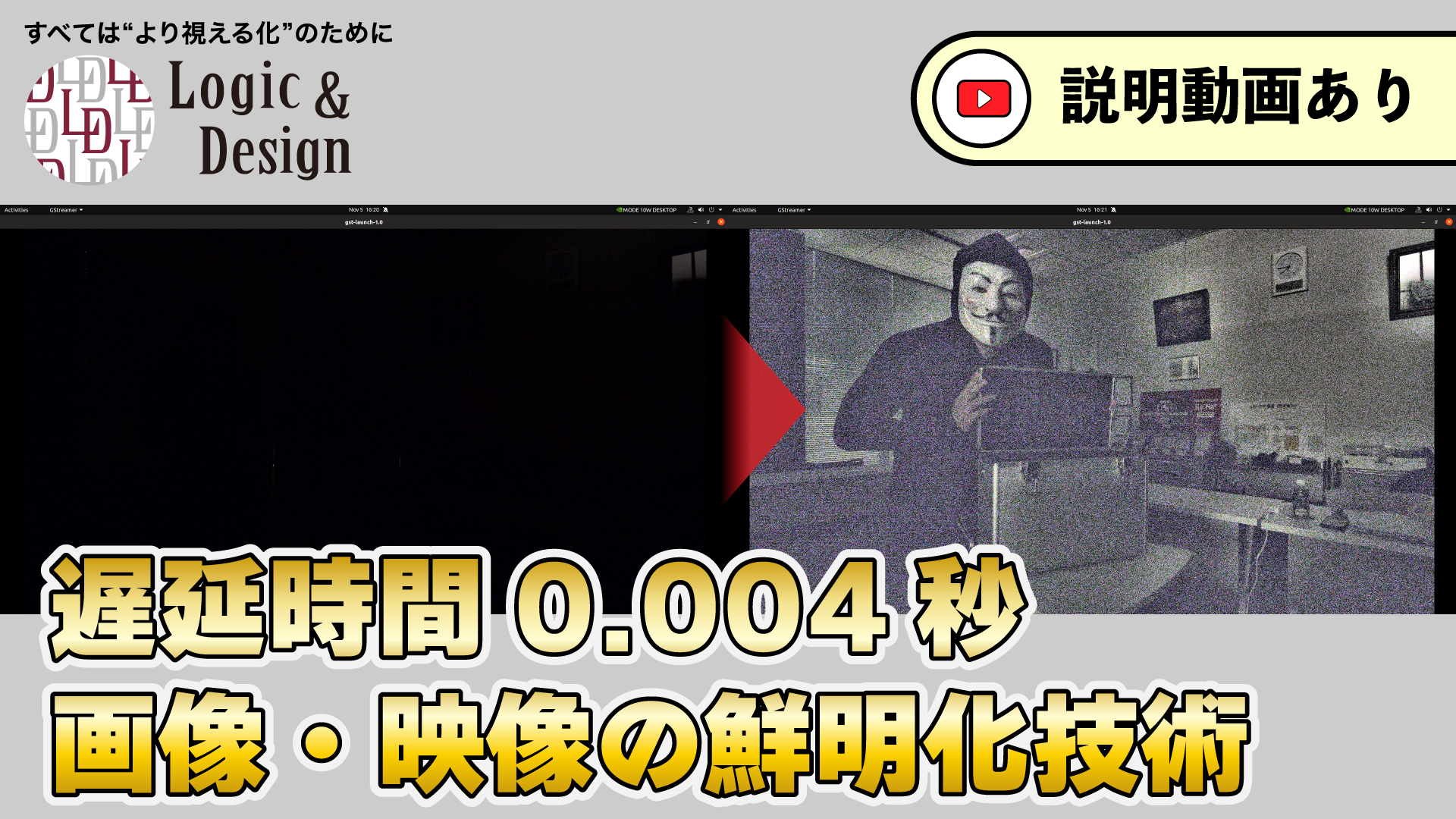
- 製品紹介
画像・映像の鮮明化
画像や映像の鮮明化技術は、防犯や医療など様々な分野で活用されており、世界をより安全にするための重要なツールです。
この技術は、リアルタイムの映像を遅延時間わずか0.004秒で自動鮮明化処理を行うことができます。
従来の鮮明化技術とのちがい
従来の鮮明化技術では、明るい部分と暗い部分が混在する画像や映像の鮮明化が難しいという課題がありました。
また、処理が重たく手間がかかることも問題でした。
ロジック・アンド・デザインの鮮明化技術の特徴
ロジック・アンド・デザインの特許技術は、各画素の情報を周囲の明度分布から最適な値に置き換えることで、鮮明な画像や映像を生成します。
この技術は、遅延時間がわずか0.004秒で、ほぼリアルタイムに鮮明化処理を行うことができます。さらに、処理が軽く、従来の方法に比べて効率的です。
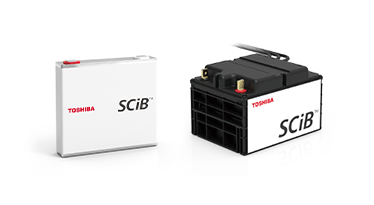
- 製品紹介
SCiB™とは?
東芝が開発したSCiB™とは、負極にチタン酸リチウムを使用した新しいタイプのリチウムイオンバッテリーです。
高い安全性と長寿命、急速充電を特徴とするSCiB™はトータルコスト削減や作業者負担の軽減、業務改善が実現できるとして
自動車・鉄道などの乗り物やAGV/AMR・ロボットをはじめとする産業機器、蓄電施設といったインフラ設備などの産業用途において注目を集めています。
従来のバッテリーと比較して、急速充電が可能であり、寒冷地でも優れた性能を発揮します。
一般的なバッテリーの課題
現在広く普及している一般的なリチウムイオン電池や鉛蓄電池には、以下のような課題があります。
-
充放電回数の制限:従来のバッテリーは充放電回数が少ないため、寿命が短い。
-
安全性の問題:発熱や発火リスクがある。
-
充電時間の長さ:急速充電が難しく、長時間の充電が必要。
-
低温環境での性能低下:寒冷地では充電や放電性能が低下しやすい。
SCiB™では、これらの課題を解決することができます。
SCiB™の特徴
SCiB™の主な特徴を以下に紹介します。
- 長寿命
SCiB™は、約20,000回以上*充放電を繰り返しても劣化が少ないです。
大規模蓄電システムのような充放電の多い用途でもメンテナンス回数が少なく環境にも貢献できます。 - 高い安全性
外部からの圧力などによって内部短絡が発生する状況においても、発煙・発火の可能性が極めて少なく
自動車、産業機器、定置用など高い安全性と信頼性が要求される様々な分野での使用が可能です。 - 急速充電
6分間で80%以上*の充電が可能であり、自動車やバス等も急速充電が可能です。
また、急速充電を繰り返しても、劣化が少なく安心して使用できます。 - 高入出力
大電流での充放電が可能なため、鉄道や自動車の減速時に発生する大きな回生電力を蓄電したり、モータの始動に必要な大電流を供給することが可能です。 - 広い動作温度範囲
低温で充電しても金属リチウムが析出しないため、-30℃*の低温環境下で繰り返し充電・放電が可能です。
-
広い実効SOCレンジ
SOC**の広い範囲に亘って高い入出力特性を持つため、SOC0~100%で使用可能です。システムの電池搭載量の削減が可能です。
*セルの種類や使用条件により特性は異なります
** SOC:State of Charge:充電状態
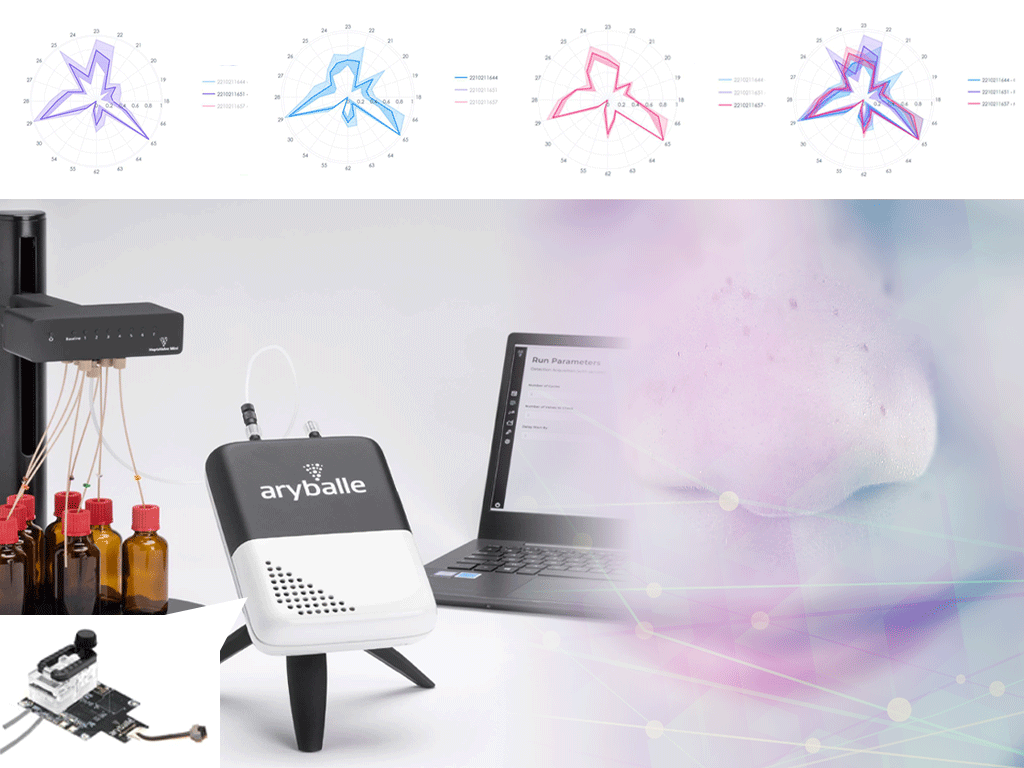
- 製品紹介
新方式においセンサーとは?
- 人間の嗅覚のようににおいの種類を検出・識別してデータ化できる
- リアルタイムで測定ができる
- 特許技術のシリコンフォトニクス式は異なるにおいを連続して測定が可能
従来のにおい測定の難しさ
においは人によって感じ方が違ったり、同じにおいを嗅ぎ続けると感覚が鈍ってしまいます。
また同じ人でもその日の体調や温湿度などの環境変化によっても感じ方が変わります。
人が一定の条件で測定することが難しい曖昧な要素です。
シリコンフォトニクス式においセンサーの特徴
においの元となる有機性揮発化合物(VOC)がバイオセンサーに付着することでバイオセンサーが反応します。
その反応をレーザーと光学センサーで捉え、においのパターンをサーバーに送信して表示・分析をすることでデジタル嗅覚として使用できます。
バイオセンサーはVOCが付着しやすく剥がれやすい特徴を持っているので、短時間で異なるにおいを計測できます。
においセンサーの活用例
- 食料品や化粧品などの製造工程では製造ロットによる品質のバラつき検知
- 原材料の品質チェック
- 新製品開発の際にかおりの時間経過による変化の観察や条件をかえたサンプルの分析
- 従来は感覚でしか表せなかったにおいについてデータを根拠にしたレポートの作成

圧着コネクタとの比較で見えたスリーエムジャパンの『ミニクランプⅢ』が製造現場を変える理由とは?
- 製品紹介
『ミニクランプⅢ』のポイント
- 4芯の結線作業がわずか14秒で完了する、専用工具がいらない画期的なセンサー用圧接コネクタ。
- 加工時間を大幅に短縮し、製造コストの削減に貢献!初心者でも簡単に使える設計。
製品の特徴
ミニクランプⅢの最大の特徴は、電線の被覆を剥く必要がない圧接方式を採用していることです。
結線に必要な時間を驚くほど短縮できます。
また、特殊な工具を必要とせず、誰でも簡単に扱える設計です。
- 4芯圧着コネクタと比較すると結線作業にかかる時間を80%以上削減可能
- 工具が不要なので作業に慣れていない人でも簡単導入
- センサー用に最適化された高い接続品質
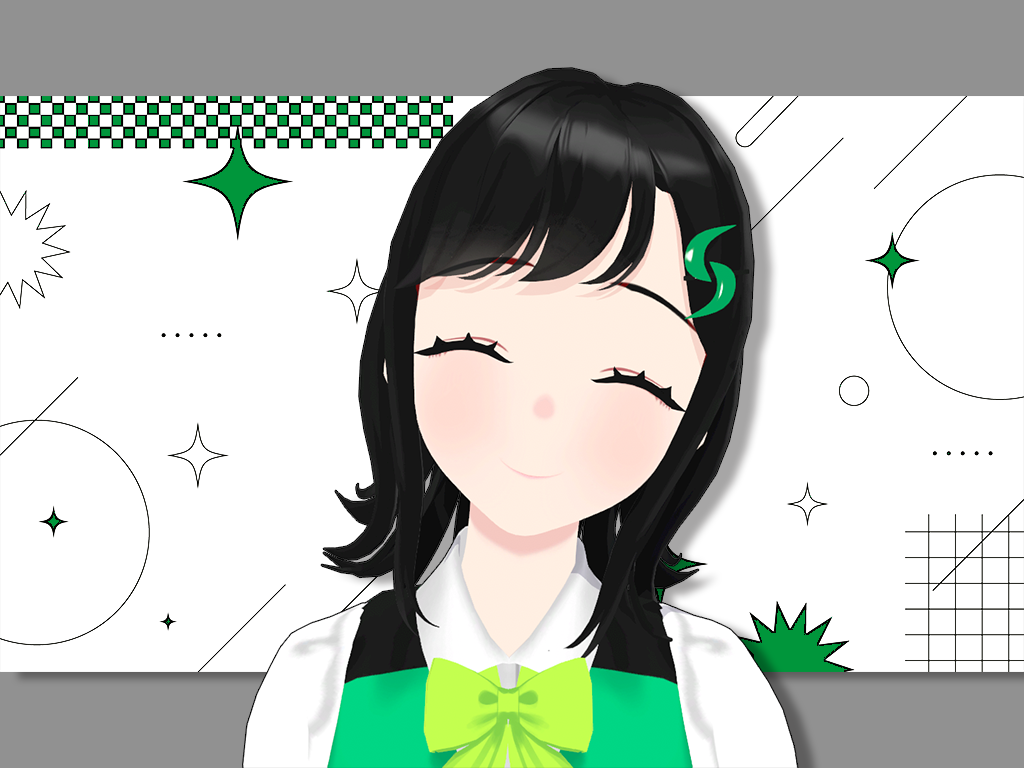
- お役立ち情報
プロフィール
お世話になっておりますサンワテクノスの三來部さんわ(みくるべさんわ)です!
まずは私について簡単にご紹介します!
- 肩書:バーチャルプロモーション担当
- 趣味:動画の制作(企画から編集まで全般やってます!)
- 座右の銘:「分かりやすく面白く!」
- 好きなこと:みなさんからの質問や感想を聞くこと。おしゃべりも大好きです♪
わたしのお仕事は?
- 主に公式YouTubeチャンネル「さんわちゃんのお仕事応援チャンネル」の運営をしています!
このチャンネルでは、製品やサービスの魅力をしっかりお届けするために、以下のような動画をお届けしています。 - 製品・サービス紹介
新しい製品やサービスの使い方や特徴について、楽しく解説します!
おなじみの製品から専門性の高いニッチなものまで、分かりやすく楽しい動画を配信しています♪ - 課題解決サポート
「こういう問題を解決したい」「こういうことで困っている」そんな課題を解決するための動画も制作しています。
御社の課題も解決できるかも! - インタビュー
製造業の企業さんにお邪魔して、ものづくりに携わっている方々に直接インタビューを行っています。
製品が生まれていく工程や、現場で行われている工夫についてお届けします!
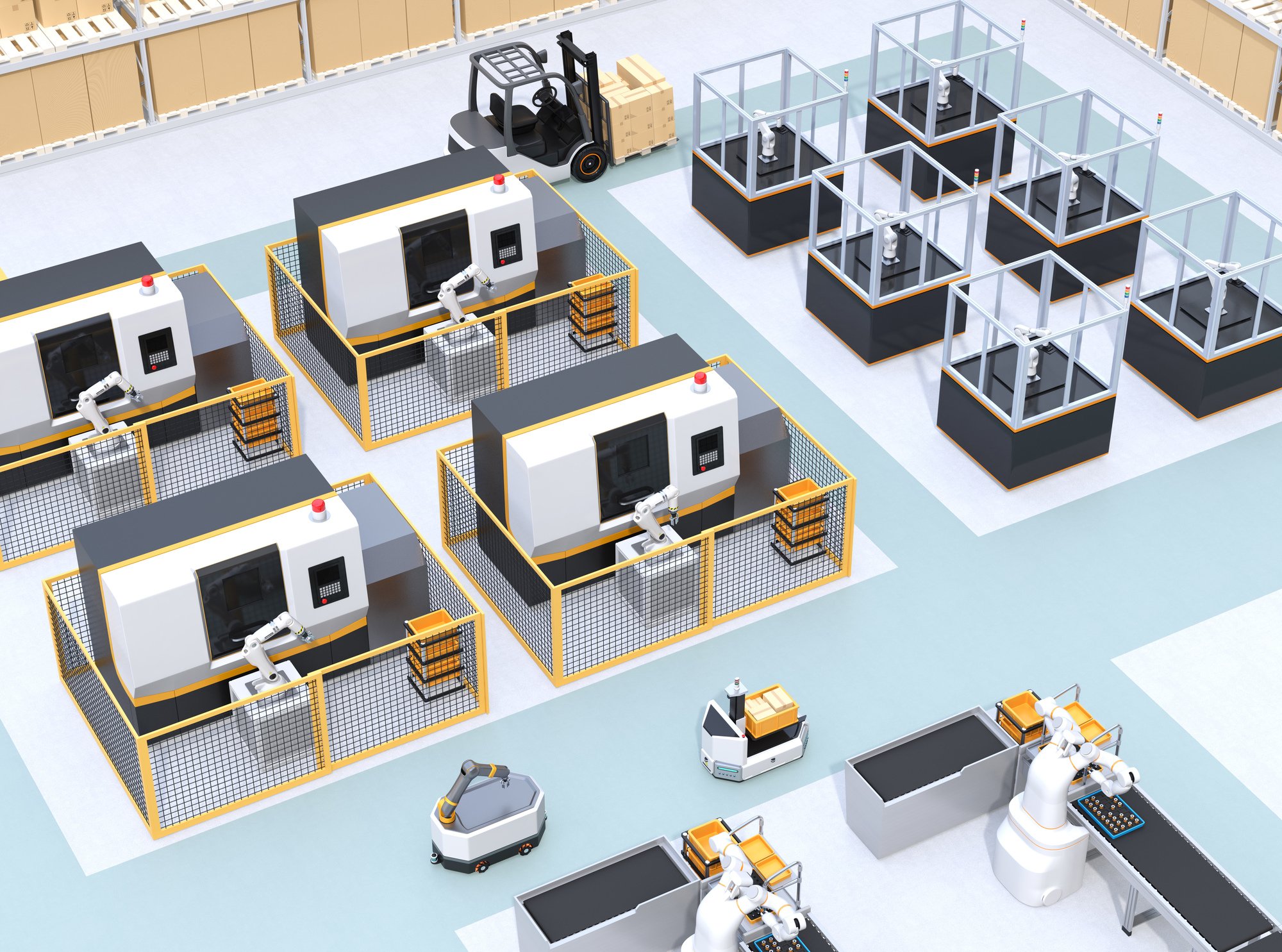
- お役立ち情報
「産業用ロボット」を導入する企業に義務付けられている「安全対策」。「労働安全衛生法」や「ISO 10218」といった法令・規定が定められており、企業はこうした法的な安全措置をとることで、作業員の安全確保や事故防止に努める必要があります。この記事では、法令や規格について述べながら、安全対策の手順や注意事項、具体的な対策例についてもご紹介します。
「産業用ロボット」の安全対策に関する基準
「産業用ロボット」の安全対策に関わる法令や規格には、「労働安全衛生法」と「ISO10218」があります。
(1)労働安全衛生法
「労働安全衛生法」では、「産業用ロボット」の設置と運用についての具体的な安全基準が定められており、安全柵の設置が義務付けられています。
“”「産業用ロボット(定格出力が80Wを超えるもの)」に接触することにより危険が生ずるおそれがあるときは、さく又は囲い等を設けること“”(労働安全衛生規則第150条の4)
安全柵は、ロボットと人の接触や事故などを未然に防ぐためのものです。ただし、リスクアセスメントを行い、作業者の安全確保が証明できれば、設置義務が免除される場合があります。例えば、センサーが取り付けられたライトカーテンや、セーフティレーザースキャナの設置など。具体的な安全対策については、記事の後半でご紹介しています。
(2)ISO 10218
「ISO 10218」は、「産業用ロボット」の安全基準について「国際標準化機構(ISO)」によって定められた規格です。ロボットの設計や製造、設置、運用について細かに規定されています。「ISO10218」を遵守することで国際的な安全基準をクリアでき、ビジネスをグローバルに広げていくアドバンテージとなります。
考えられるリスク
産業用ロボットの運用においては、以下のような具体的なリスクが考えられます。
(1)自動運転中の作業者の侵入
ロボットの可動範囲に作業者が誤って侵入することで、大けがを負う可能性があります。このリスクを低減するためには、センサーを設置し、作業者が侵入した場合にロボットが停止するようにする必要があります。
安全対策・リスクアセスメントを行う際の注意点
産業用ロボットの安全対策やリスクアセスメントを実施する際には、以下の注意点に留意することが重要です。
(1)危険源の特定
産業用ロボットのリスクアセスメントでは、まず危険源を特定することが重要です。新たに機械を新設・改造する際に、潜在的な危険源を洗い出し、それがどのような危害をもたらすかを評価します。
(2)リスク評価の正確性
リスク評価は、危害の発生確率とその影響の程度を正確に評価することが求められます。評価が不十分だと、重大なリスクが見逃される可能性があります。
(3)適切なリスク低減策の実施
特定されたリスクに対しては、本質安全対策や安全防護対策を講じる必要があります。具体的には、セーフティセンサーの設置や安全柵の設置などが挙げられます。
(4)作業手順書と教育の見直し
リスクアセスメントの結果に基づいて、作業手順書の見直しや社員への教育を行い、リスク低減策が確実に実施されるようにします。
(5)フィードバックと継続的な改善
実際の運用中に新たなリスクが発見された場合、フィードバックを基にリスクアセスメントを再度実施し、継続的に改善を図ることが重要です。
(6)法規制の遵守
リスクアセスメントは、労働安全衛生法やISO規格などの法規制に基づいて実施する必要があります。これにより、法的要求事項を満たし、安全性を確保します。
(7)メンテナンス時の安全確保
ロボットのメンテナンス時には、可動部の接触などのリスクがあるため、安全ハーネスの使用や作業手順の見直しが必要です。
これらの注意点を踏まえて、産業用ロボットのリスクアセスメントを徹底することで、労働者の安全を確保し、けがや事故を未然に防ぐことができます。
「産業用ロボット」の安全対策の例
ここからは、具体的な安全対策の事例をご紹介します。
(1)安全柵の設置
「産業用ロボット」を導入するにあたり、最も普及している安全対策です。ロボットのまわりに柵や囲いを設置し、人とロボットを隔離します。安全柵の設置には、以下のようなポイントがあります。
○ 法令遵守:労働安全衛生法および労働安全衛生規則に準拠した設置が必要です。特に、定格出力が80Wを超える産業用ロボットで、接触により危険が生じるおそれがある場合は、柵または囲いの設置が義務付けられています。
○ リスクアセスメントの実施:安全柵の設置前に、作業環境や作業内容に基づいたリスクアセスメントを行い、適切な安全対策を選択することが重要です。
○ 人とロボットの作業エリアの明確な分離:安全柵は、人の作業場所とロボットの可動範囲を明確に分離するように設置する必要があります。
○適切な材質の選択:例えば、食品工場などでは衛生面を考慮し、ステンレス製の安全柵を選択するなど、作業環境に適した材質を選ぶことが重要です。
○ メンテナンス性の考慮:定期的な点検や清掃が容易に行えるよう、アクセスしやすい構造の安全柵を選択することが望ましいです。
○国際安全規格への適合:EN ISO12100、EN ISO13857、EN ISO10218-2などの国際安全規格に適合した安全柵を選択することが推奨されます。
○作業効率への配慮:安全柵の設置が他の作業に支障をきたさないよう、設置スペースや作業動線を考慮する必要があります。
○ 補完的な安全装置の併用:必要に応じて、ライトカーテンやセーフティレーザスキャナなどの安全装置を併用し、より高度な安全性を確保することも検討すべきです。
これらのポイントを考慮しながら、作業環境や作業内容に応じた適切な安全柵の設置を行うことが重要です。また、安全柵の設置後も定期的な点検とメンテナンスを行い、常に安全性を維持することが求められます。
(2)ライトカーテン
安全柵により安全性が確保されていても、人が立ち入るための開口部やドアが設置されている場合には、ライトカーテンやドアスイッチが、侵入を検知する設備として用いられます。
こうした対策を講じていても、安全柵の内側に人がいる時にロボットが作動し、怪我や事故が発生するリスクも考えられます。特に事故要因として挙げられるのが、設備の死角。設備が大きくなるほど死角が増え、そこに人がいるのに気づかないままロボットを起動してしまうというものです。これを防ぐために、「起動および再起動」時の安全性について、「ISO10218-2」ではこのように規定されています。
○起動及び再起動の制御機器は、安全防護空間外に配置し、手動で操作されなければならない
○オペレータは、各制御位置から、安全防護空間内に誰もいないことが確実に確認できなければならない
○これが現実的でない場合には、安全防護空間のいたる所にオペレータを検知するための存在検知を備えなければならない
つまり、安全性を確保するためには、設備の死角に人がいないかどうかを検知した上で、ロボットを起動させる必要があります。この解決手段として、「レーザースキャナ」が挙げられます。
(3)セーフティレーザースキャナ
前述した安全性確保においても、安全柵を設置せずに対策を講じる場面でも、人の存在を検知するための機器が必要です。その一つが、「セーフティレーザースキャナ」です。最新の「セーフティレーザースキャナ」は、従来の製品に比べて検知する領域が広くなったり、誤検知などの作動不良が改良されたりと、実用性の高い製品が誕生しています。
豊富なネットワークを強みに、工場の課題解決に貢献するサンワテクノス。
「産業用ロボット」を導入している企業にとって、「労働安全衛生法」や「ISO10218」で定められている安全対策の遵守は義務です。安全性を確保しながらも、生産性の向上や品質の安定をはかることで、さらなる事業拡大が期待できるでしょう。サンワテクノスでは、メーカーと連携しながら、製造現場における課題やご要望のヒアリング、技術的なご提案、導入にいたるまで一貫した技術支援を行っております。「産業用ロボット」の安全対策についてご検討されている企業様は、ぜひお気軽にお問合せくださいませ。
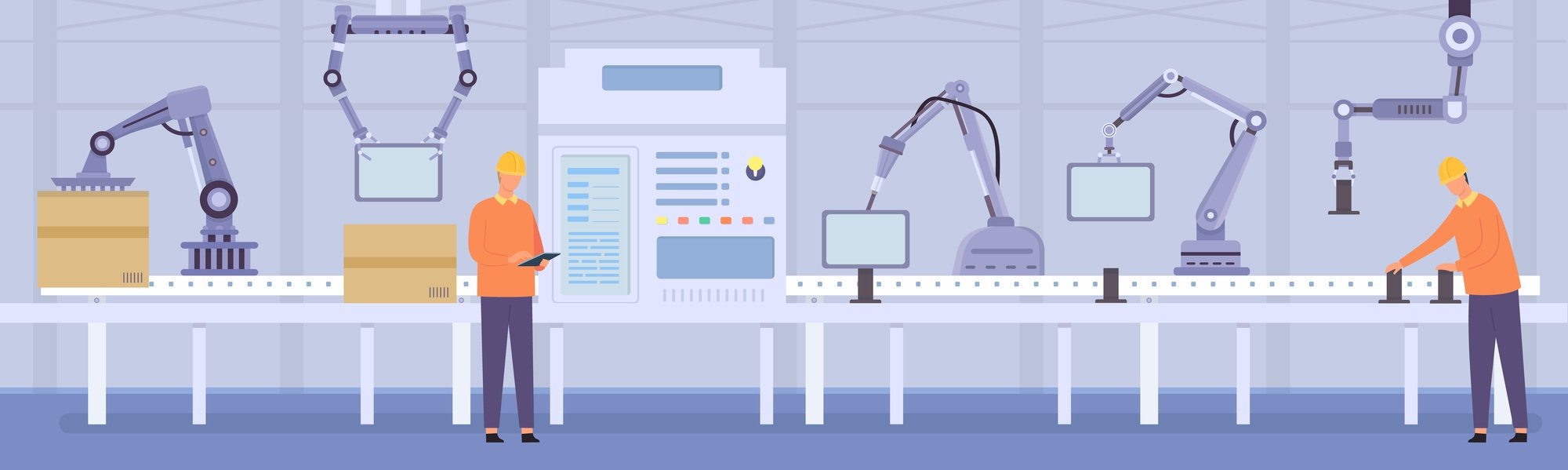
- お役立ち情報
人件費削減や人手不足の解消、安全の確保や作業における柔軟性といった観点から、工場の様々なニーズに応える存在として、多くの製造現場で導入が進められている「協働ロボット」。この記事では、「産業用ロボット」との違いや「協働ロボット」導入にあたってのメリット・デメリット、必要となるコストや導入手順などについてご紹介します。
協働ロボットとは
協働ロボットは、人間と協力して作業を行うように設計されたロボットです。これらのロボットは、安全機能が組み込まれており、人間と同じ空間で作業することが可能です。協働ロボットは、製造業や物流業、医療分野などで使用され、人間の作業を補完し、生産性を向上させることを目的としています。特徴としては、柔軟性、安全性、簡単なプログラミングなどが挙げられます。
【メリット】省スペースで、人との分業が可能。誰でも扱いやすい。
協働ロボットには様々な導入メリットが挙げられます。
(1)人との協働作業が可能
協働ロボットは、人と同じ作業スペースで安全に作業できるため、生産ラインに並んで単純作業や反復作業を行うことができます。これにより、人とロボットの効率的な分業が可能になります。
(2)柔軟な運用
協働ロボットは移動が容易で、日替わりで作業内容や場所を変更できます。これにより、タクトタイムの超過している作業部分に柔軟に対応できます。
(3)安全柵いらず
安全柵を設置し、作業員との距離を確保する必要がある「産業用ロボット」とは違い、「協業ロボット」は人の安全を考慮した設計となっているため安全柵を設置する必要がありません。そのため、限られたスペースであってもロボットを設置できたり、移動させたりすることも可能です。また、協働ロボットは人がいる空間での作業に用いられるため、特定の製品の製造にのみ使用したり(もしくは使用しない)、作業員と分担して作業を行うことにより、設備費のイニシャルコストが削減できる可能性もあります。こうしたメリットから、特に小ロット・多品種の製造現場などにおいて、協働ロボットは実用的な機器だといえるでしょう。
(4)専門のエンジニアがいなくてもOK
専門のエンジニアがいないから、ロボットの導入にハードルを感じている。そんな企業様も少なくないでしょう。協働ロボットは、ロボット操作に不慣れな人でも直感的に操作しやすいように、機能面の開発も進んでいます。具体的には、ロボットに動作を教える「ティーチング」が専門のエンジニアではない人でもできるようになっていたり、「ハンドユニット」さえあれば、専門業者を呼ばなくても自社でロボットの動作をカスタマイズできるようになっていたり。このように協働ロボットは、特定の技術者だけが扱えるロボットではなく、「誰でも扱いやすい」ロボット。協働ロボットを導入することにより、活用アイデアが生まれたり、生産性の向上が期待できたりと、製造を加速させる起点になるといえます。
【デメリット】協働ロボットの特性による対応力の限界。
「協働ロボット」はメリットだけでなく、デメリットもあります。
(1)動きが遅い
協働ロボットは、人がいる空間で作業し、人に接触しても安全に停止することを前提に設計されているため、「産業用ロボット」よりも動くスピードが一定以下に設定されています。しかし製品によっては、“協働モード”と“産業用ロボットモード”の切り替え機能付きの協働ロボットも開発されており、場面や用途によって使い分けも可能です。センサーと連動し、人が近くにいない場合は“産業用ロボットモード”でスピーディに動作し、人が近くにいたら“協働モード”で安全性を優先する。こうした使い分けにより、安全性を確保しながら作業効率を高めることができます。
(2)パワーに限界がある
協働ロボットの可搬重量は製品によって様々ですが、500g~30kgのものが多く、産業用ロボットに比べるとパワー不足が懸念されます。しかし捉え方を変えれば、これまで作業員が行っていたピッキングや部品の取り付けなど、パワーが必要のない作業については、協働ロボットで代用可能です。近年は30kgの可搬タイプも市場に出回りはじめ、パレタイズ作業にも協働ロボットを活用している事例もあります。
(3)高価格
安全性の確保や、専門性がなくても作業できる使い勝手の良さなど、様々なメリットがありつつも、協働ロボットの普及率は産業用ロボットに比べて低いのが現状です。各軸に力学センサーを内蔵していることから製品が高価格であることも、その一因にあると考えられます。しかし、今後のロボット開発の進歩により、製品のコストダウンや普及率の向上も十分に見込めるでしょう。
協働ロボットの導入ステップ
協働ロボットの導入にあたり、以下の手順を踏むことで導入が円滑に進みます。
(1)潜在的ニーズの発掘と課題の明確化
現状の作業工程を見直し、潜在的なニーズを発掘します。そして、解決すべき具体的な課題を明確にします。
(2)導入目的の設定
課題に基づいて、協働ロボット導入の具体的な目的を設定します。例えば生産性向上、品質改善、作業員の負担軽減などが該当します。
(3)適切なロボットの選定
業務別のニーズに合ったロボットを選定します。作業内容や目的に応じて、ロボット本体やアームの動かし方などを検討します。
(4)システム設計
ロボット設計、安全設計、周辺設計、制御・センシング設計を行います。これには生産ラインの構築や安全規格に沿った設計も含まれます。
(5)リスクアセスメントと安全対策
ロボット導入により発生するリスクを解析し、必要な安全対策を講じます。
(6)プロジェクト・マネージメント
計画段階から運用開始まで、プロジェクト全体を管理します。
(7)導入とテスト
設計に基づいてロボットを導入し、実際の運用環境でテストを行います。
(8)教育・トレーニング
ロボットを操作する作業員に対して、必要な教育やトレーニングを実施します。
(9)運用開始と評価
実際の運用を開始し、導入目的が達成されているか評価します。
これらのステップを適切に実行することで、協働ロボットの効果的な導入が可能になります。また、初めての導入や専門知識が不足している場合は、ロボットシステムインテグレータ(SIer)のサポートを受けることも有効です。
協働ロボットの導入に必要なコスト
協働ロボットの導入には、本体価格以外にもさまざまなコストがかかります。主に、以下の費用が挙げられます。
(1)協働ロボット本体
一般的に200万円〜500万円程度です。ただし、最近では100万円台の低コストモデルも登場しています。
(2)周辺機器
○グリッパーやセンサーなどのロボットに直接取り付ける装置
○ロボット架台
○ベルトコンベアや加工機などの生産ライン構築に必要な設備
○PLC (プログラマブルロジックコントローラ)
(3)システムインテグレーション (SIer) 費用
ロボットの導入から稼働までをサポートするSIer会社への支払いです。コンサルティング、設計、周辺機器の手配、システムの組み立て、ティーチングなどが含まれます。
(4)人材教育・育成費用
ロボットの操作やメンテナンスを行う担当者の教育にかかる費用。
(5) 安全対策費用
リスクアセスメントや安全装置の導入にかかる費用。
具体的な総コストは、導入する環境や目的によって大きく異なりますが、ロボット本体価格の数倍以上になることが多いとされています。協働ロボット導入の費用対効果は、単純な費用だけでなく、生産性・品質向上などの直接的メリットや、人材採用・教育コスト削減、離職リスク回避などの間接的メリットも含めて、広い視野で検討することが重要です。
豊富なネットワークを強みに、工場の課題解決に貢献するサンワテクノス。
人手不足の解消や安全性の確保、生産性向上など、製造現場をとりまく様々な課題やテーマに対して価値を発揮する「協働ロボット」。サンワテクノスでは、メーカーと連携しながら、製造現場における課題やご要望のヒアリング、技術的なご提案、導入にいたるまで一貫した技術支援を行っております。「協働ロボット」の導入をご検討されている企業様は、ぜひお気軽にお問合せくださいませ。
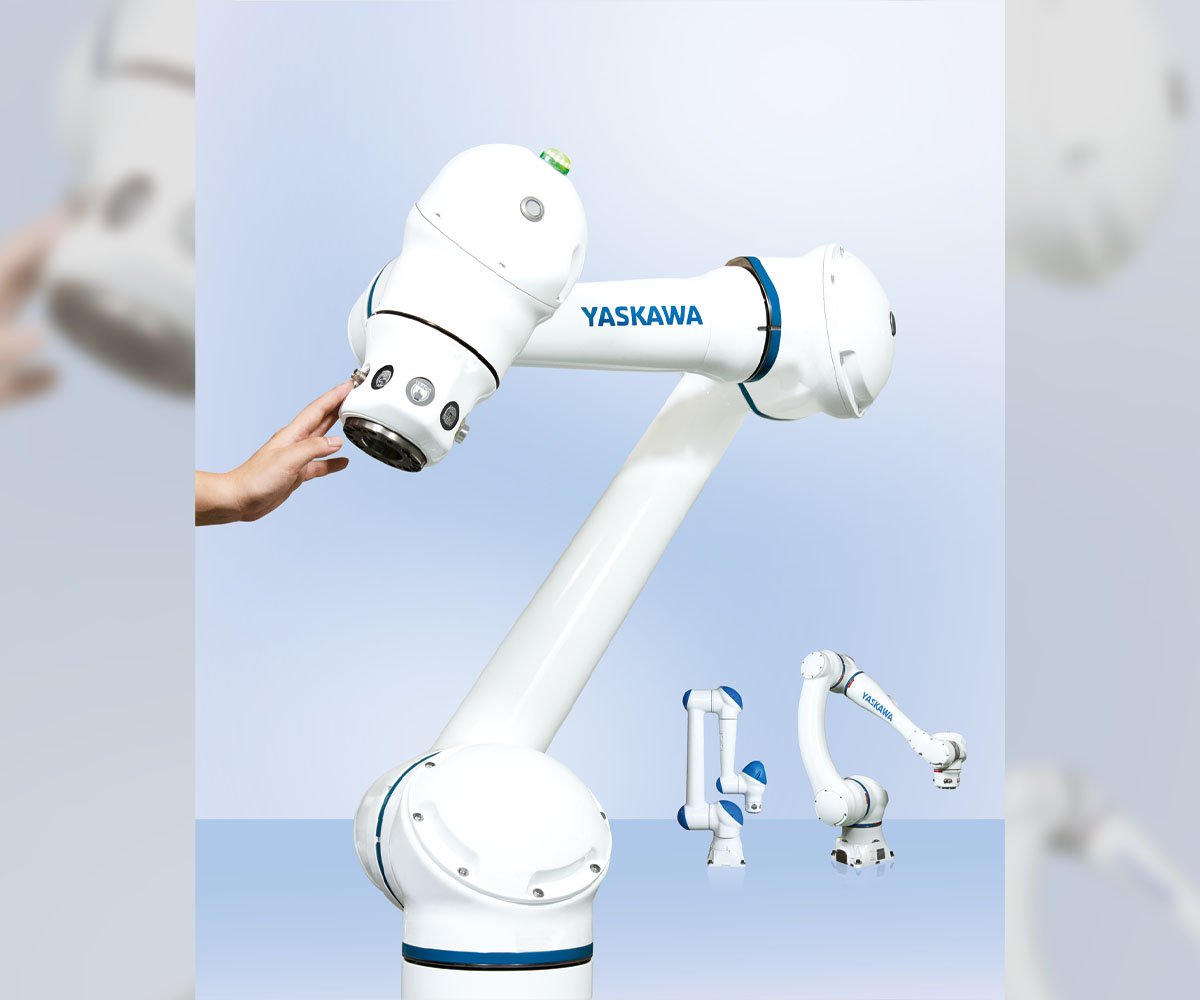
- 製品紹介
「産業用ロボット」とは違って、安全柵がなくても作業員がいるスペースで安全に協働できるよう設計されている「人協働ロボット」。作業員の仕事を分担し、補助する「人協働ロボット」は、作業員の安全確保や人手不足の解消など、製造現場の様々な課題解決や品質向上に価値を発揮する機器です。この記事では、サンワテクノスの取り扱い製品である安川電機製の「人協働ロボット MOTOMAN-HCシリーズ」について、その特徴をご紹介します。
安全柵は必要なし!限られたスペースでも設置可能。
安全柵の設置義務があり、導入するには広いスペースの確保が必要な「産業用ロボット」に比べて、「人協働ロボット MOTOMAN-HCシリーズ」は、既存の作業環境での導入が可能です。その理由は、ロボットに搭載されている安全機能。「産業用ロボット」のように安全柵を設置することも、広いスペースの確保も不要で、導入しやすいというメリットがあります。
※「人協働ロボット MOTOMAN-HCシリーズ」は産業用ロボットのための安全要求事項を定める国際規格「ISO10218-1(日本産業規格ではJIS B 8433-1に該当)」に準拠しています。また、ロボットコントローラの「安全機能」は,国際規格「ISO 13849-1PLd(Cat.3)」に適合しており、第三者認証機関より安全認証を取得しています。これらの安全機能により、HCシリーズは安全柵なしのシステム構築が可能ですが、全てのケースにおいてお客さまにてリスクアセスメントを実施する必要があります。
怪我や事故を防ぐ、人にやさしい安全設計。
「人協働ロボット MOTOMAN-HCシリーズ」は、作業員の近くで作動させることを前提とした安全設計。人や物に触れるとすぐに安全に停止したり、一定のスピード以下に動きをコントロールしたり、ロボットに物が挟まれても取り出せるように自動で動いたりと、怪我や事故を引き起こさないための機能が充実しています。ロボットの構造や形状そのものも、安全性にもとづく設計で、作業員の安全を確保します。
※ISO20318-1/ISO13849-1第3者認証取得
初心者でも操作かんたん。タブレット感覚で教示できる。
専門のエンジニアがいないから、導入が難しい。ロボットの扱いに慣れていないから、うまく操作できるか不安。「人協働ロボット MOTOMAN-HCシリーズ」なら、そうした心配は無用です。従来の「産業用ロボット」は、専門のエンジニアによるティーチングが必要なのに比べて、「人協働ロボット MOTOMAN-HCシリーズ」はロボット操作に慣れていない人でも、およそ30分でピックアンドプレイス動作のティーチングが習得できます。それを可能にしているのが、タブレット感覚で操作できるスマートペンダント。直感的にロボットを操作できるように工夫されており、専門的なエンジニアが不在でも、安心してロボットを導入・活用できます。
使用用途に合わせた豊富なラインナップ。
「人協働ロボット MOTOMAN-HCシリーズ」は、多様な仕様の製品を取りそろえています。水・切削油などの液体や、切りくずなどの粉じんにさらされる環境においても使用できる防じん・防滴仕様や食品仕様。大型ワークの搬送や複数ワークの搬送作業にも適用可能な高可搬タイプ。豊富なラインナップで、多様な作業環境のものづくりをアシストします。
豊富なネットワークを強みに、工場の課題解決に貢献するサンワテクノス。
作業員の安全を確保しながら、従来の作業環境に導入可能な「人協働ロボット MOTOMAN-HCシリーズ」。人手不足の解消や工場の自動化など、課題解決をサポートする技術や機能が搭載されており、ものづくりをよりスマートに後押しします。サンワテクノスでは、株式会社安川電機と連携しながら、製造現場における課題やご要望のヒアリング、技術的なご提案、導入にいたるまで一貫した技術支援を行っております。「人協働ロボット MOTOMAN-HCシリーズ」についてご興味のある企業様は、ぜひお気軽にお問合せくださいませ。
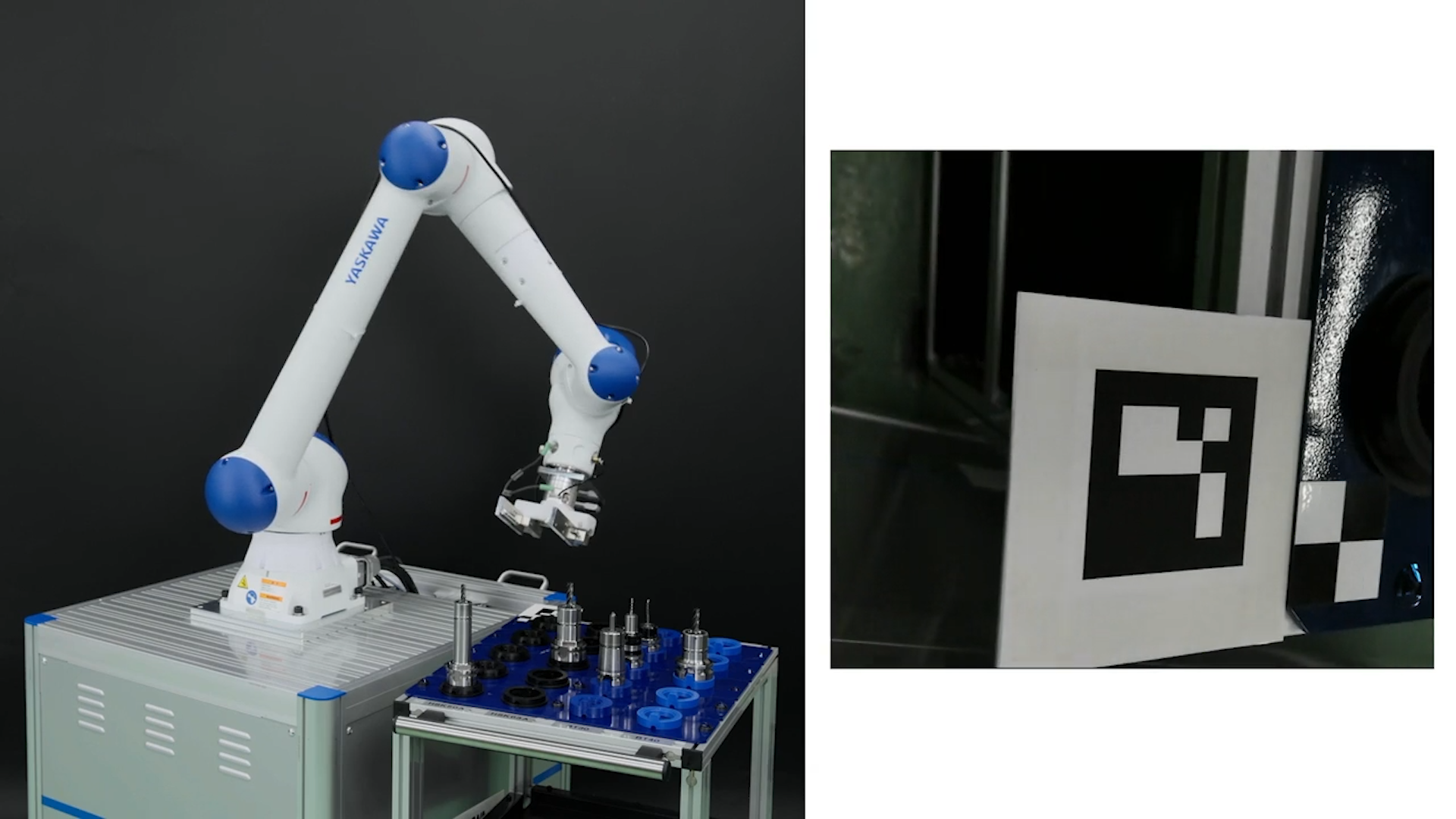
- 製品紹介
労働力不足への対応や、生産性の高い多品種変量生産の実現。ものづくりにおける課題を解決し、品質向上を達成するにはデジタルマニュファクチャリングの推進が欠かせません。サンワテクノスは株式会社エムテックとの協働で、仮想空間を活用したデジタルマニュファクチャリングを実現するロボットソリューションパッケージ「3D Connect シリーズ」を開発・発売しています。この記事では、その第一弾目の製品であるAR マーカーを利用したロボットソリューションパッケージ「AR^2 System(エーアール・ツー・システム)」についてご紹介します。
「3D Connect シリーズ」は、三次元CADとロボットなどのモーションコントローラーをリアルタイムに連携操作させるプロセスシミュレーター「Planning Simulator」を用いて、設計から動作に至る各種機能を持ったモジュールを組み合わせたソリューションパッケージです。 これにより、ロボット動作における現実と仮想空間の座標の齟齬が補正され、ものづくりにおけるデジタルマニュファクチャリングが促進されます。
標準的なロボットは、ロボット座標で管理を行うため、対象物との相対位置がずれると再度ティーチングを行う必要があります。「AR^2 System」では、ロボットに搭載したカメラが AR マーカーを読み取り、自動座標定位を行うことで高精度にロボットの相対的位置を補正。ロボットが移動しても、ARマーカーからの相対距離で作業を行います。そのため正確な位置決めが不要になり、必要な場合にのみロボットを設置して作業させたり、移動して作業をさせたりすることも、AR マーカーを用いることで容易に可能となります。
「AR^2 System」の機能拡充とさらなる利便性の向上を目指し、オプションで追加できる機能を開発中です。同一のカメラを利用してパターンマッチングなどの画像処理を行ったり、コンベヤトラッキングなどの機能を追加したりと、一つのカメラで複数の機能を果たします。これは位置認識のみを行う既存製品との大きな違いです。
システムの立ち上げは、パソコンにロボットコントローラーとカメラを接続すれば準備完了。初期設定もウィザードに従うだけで簡単にできます。これまでロボット導入にハードルを感じていた企業様にとっても、容易に導入が可能です。
ロボット導入へのハードルを下げ、生産性向上に貢献する「AR^2 System」。単に自動化するためだけのロボットではなく、ロボット自身が自由に移動し、ワーク自体が移動した時点でもロボットとの相対関係を認識して補正できるアプリケーションで、製造現場の高度なニーズに応えます。サンワテクノスでは、株式会社エムテックと連携しながら、製造現場における課題やご要望のヒアリング、技術的なご提案、導入にいたるまで一貫した技術支援を行っております。ご興味のある企業様は、ぜひお気軽にお問合せくださいませ。
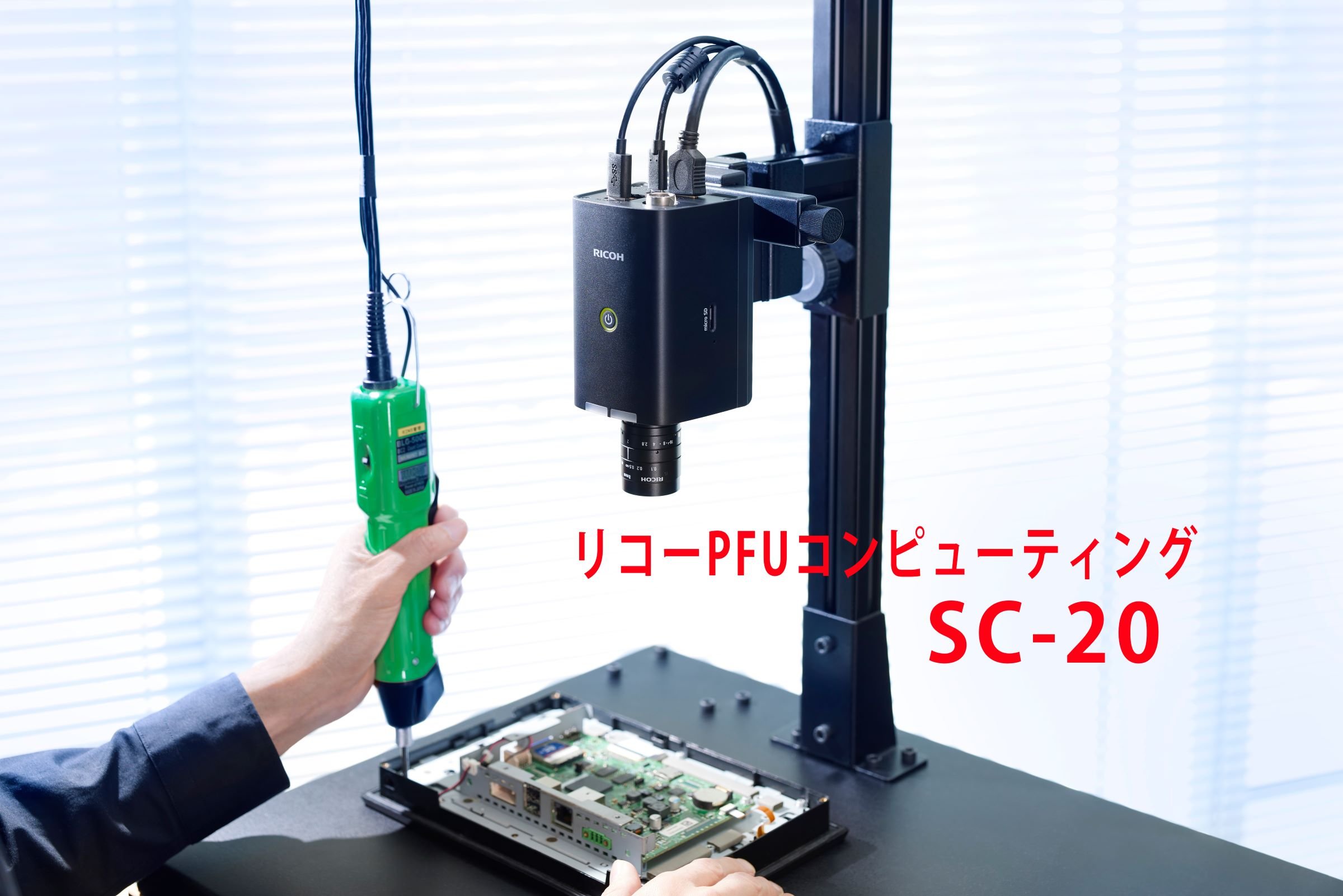
- 製品紹介
製品概要
リコーPFUコンピューティングの SC-20は、組立工程における作業ミスをリアルタイムで検出する作業検査カメラです。従来の目視検査では困難だった小型部品の取り付け状況や取り付け方向のチェック、質感マッチング判定による不織布やスポンジなどの有無検査が可能です。これにより、手作業工程の品質向上と不良低減、トレーサビリティチェックなど期待できます。また低価格でありつつ多機能であり、PCも不要なためトータルコストを抑えて導入できます。
こんなお困りはありませんか?
-
DX機器を導入したいけど設置できる人材がいない
→パソコン不要の簡単設置で誰でも簡単にセッティング可能。
-
チェック漏れが多発する
→リアルタイム検査でOK判定にならないと次工程に進まないのでチェック漏れが防げる。
-
作業者によって作業品質がばらついてしまう
→作業品質チェック機能を搭載。人による作業品質ばらつきを抑える。
-
作業効率があがらない
→作業時間の制限や品質管理を同時に行い作業効率を上げる。
-
トレーサビリティが確保できていない
→デジタルで蓄積データを管理しているので、後追いが可能。
-
高額な設備導入費用をかけられない
→制御にパソコンを使用しないため、トータル的にリーズナブルに導入が可能。
導入メリット
-
品質の均一化
目視検査のばらつきを抑制し、作業品質の均一化が図れます。 -
作業効率の向上
リアルタイムでの検査により、作業後の再検査の手間を削減できます。 -
トレーサビリティの確保
検査結果を画像ログとして保存し、作業分析やトレーサビリティに活用できます。
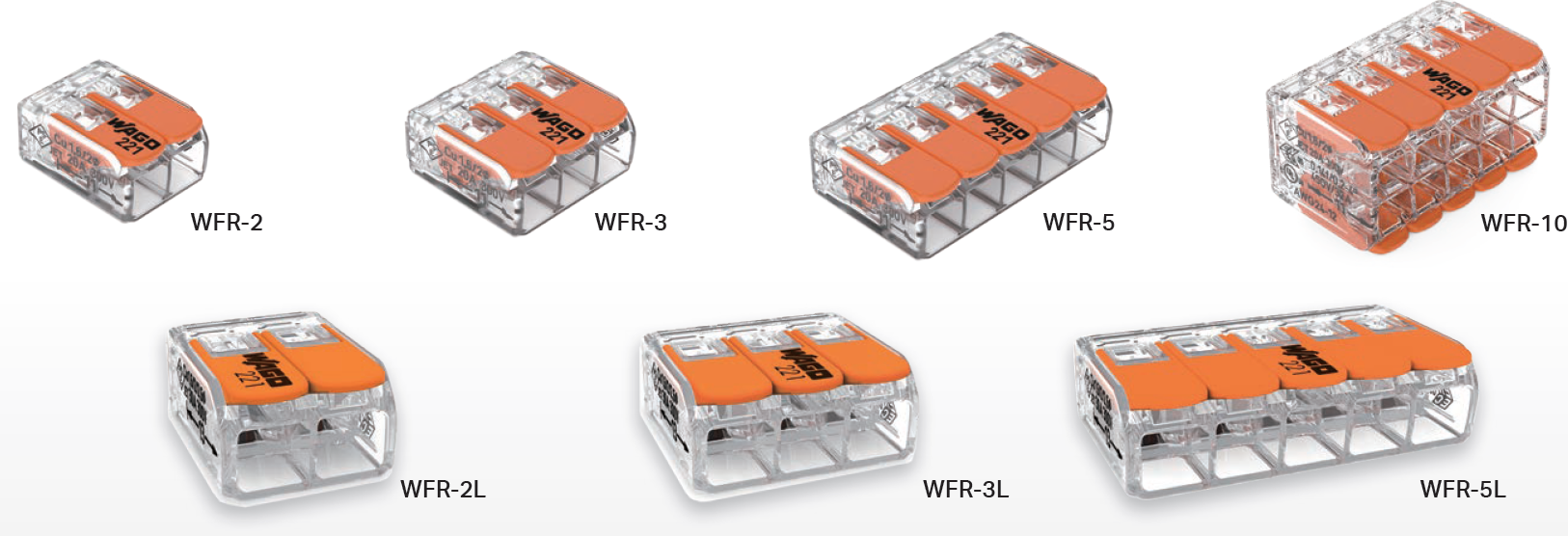
- 製品紹介
ワンタッチコネクタWFR/WFR-Lシリーズ
WAGOのワンタッチコネクタWFR/WFR-Lシリーズは、配線作業を簡単かつ安全に行うための革新的な製品です。
透明ハウジングやソフトなレバー操作など、多くの特長を持つこのシリーズは、屋内配線や一般電気工作物など、さまざまな用途に対応しています。
本記事では、WFR/WFR-Lシリーズの特長や使用方法、製品ラインナップについて詳しく紹介します。
WFR/WFR-Lシリーズの特長
-
透明ハウジング
WFR/WFR-Lシリーズの透明ハウジングは、結線状態を目視で確認できるため、安心して使用できます。これにより、結線ミスを防ぎ、安全性が向上します。 -
対応電線
このシリーズは、単線、IV7本より線、可とうより線の混在使用が可能です。幅広い電線に対応するため、さまざまな配線作業に適しています。 -
操作性
ソフトなレバー操作で簡単に結線できるため、作業効率が大幅に向上します。レバーを押し上げて電線を挿入し、押し下げるだけで結線が完了します。 -
用途
WFR/WFR-Lシリーズは、屋内配線や一般電気工作物など、さまざまな配線作業に使用可能です。内線規程や公共建築工事標準仕様書にも適合しており、信頼性の高い製品です。
結線方法
ステップバイステップガイド
- 電線の準備:ストリップゲージで電線の長さを確認し、正しい長さにむき出します。
- レバー操作:レバーを押し上げて電線挿入口を開きます。
- 電線の挿入:むき出した電線を突き当たるまで差し込みます。
- 結線完了:レバーを押し下げて結線を完了させます。
- 確認:電線を軽く引っ張り、抜けないことを確認します。
注意点
• 指を挟まないように注意する。
• 差し込みが不十分だと導通不良や発熱の恐れがあるため、正しい剥き長さでしっかりと差し込む。
メリット
WFR/WFR-Lシリーズを使用することで得られるメリットを以下にまとめます。
- 安全性の向上:透明ハウジングにより、結線状態を目視で確認できるため、結線ミスを防ぎます。
- 作業効率の向上:規定の長さに電線をむいてレバー操作するだけで、簡単に結線できるため、作業時間を短縮できます。
- 多用途対応:単線、IV7本より線、可とうより線の混在使用が可能で、さまざまな配線作業に対応します。
- 信頼性:内線規程や公共建築工事標準仕様書に記載があるため、信頼性の高い配線が求められる場所でも安心して使用できます。
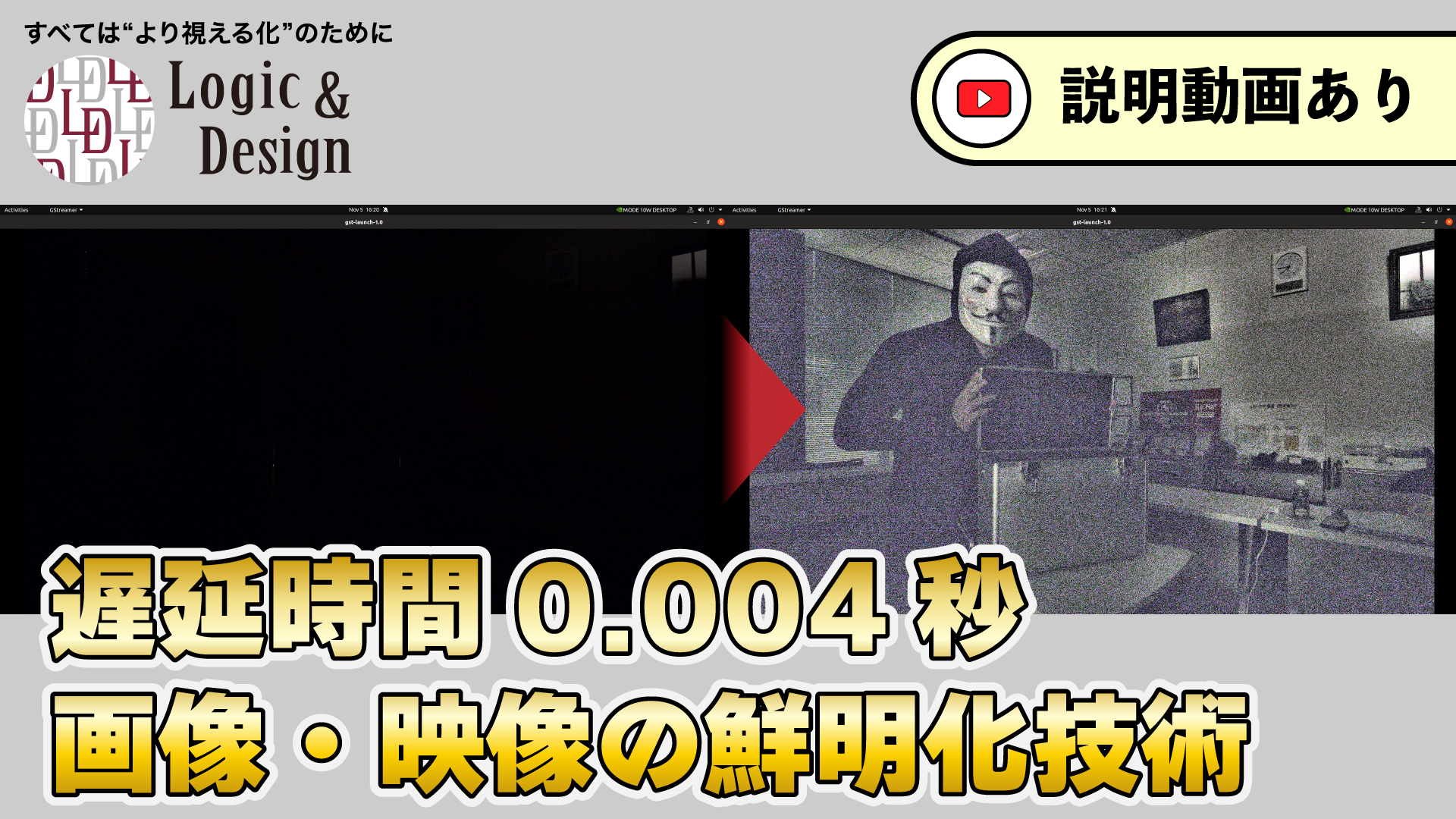
- 製品紹介
画像・映像の鮮明化
画像や映像の鮮明化技術は、防犯や医療など様々な分野で活用されており、世界をより安全にするための重要なツールです。
この技術は、リアルタイムの映像を遅延時間わずか0.004秒で自動鮮明化処理を行うことができます。
従来の鮮明化技術とのちがい
従来の鮮明化技術では、明るい部分と暗い部分が混在する画像や映像の鮮明化が難しいという課題がありました。
また、処理が重たく手間がかかることも問題でした。
ロジック・アンド・デザインの鮮明化技術の特徴
ロジック・アンド・デザインの特許技術は、各画素の情報を周囲の明度分布から最適な値に置き換えることで、鮮明な画像や映像を生成します。
この技術は、遅延時間がわずか0.004秒で、ほぼリアルタイムに鮮明化処理を行うことができます。さらに、処理が軽く、従来の方法に比べて効率的です。
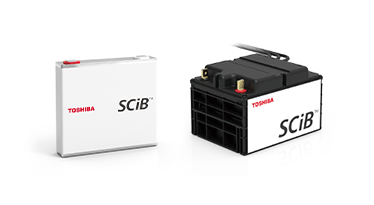
- 製品紹介
SCiB™とは?
東芝が開発したSCiB™とは、負極にチタン酸リチウムを使用した新しいタイプのリチウムイオンバッテリーです。
高い安全性と長寿命、急速充電を特徴とするSCiB™はトータルコスト削減や作業者負担の軽減、業務改善が実現できるとして
自動車・鉄道などの乗り物やAGV/AMR・ロボットをはじめとする産業機器、蓄電施設といったインフラ設備などの産業用途において注目を集めています。
従来のバッテリーと比較して、急速充電が可能であり、寒冷地でも優れた性能を発揮します。
一般的なバッテリーの課題
現在広く普及している一般的なリチウムイオン電池や鉛蓄電池には、以下のような課題があります。
-
充放電回数の制限:従来のバッテリーは充放電回数が少ないため、寿命が短い。
-
安全性の問題:発熱や発火リスクがある。
-
充電時間の長さ:急速充電が難しく、長時間の充電が必要。
-
低温環境での性能低下:寒冷地では充電や放電性能が低下しやすい。
SCiB™では、これらの課題を解決することができます。
SCiB™の特徴
SCiB™の主な特徴を以下に紹介します。
- 長寿命
SCiB™は、約20,000回以上*充放電を繰り返しても劣化が少ないです。
大規模蓄電システムのような充放電の多い用途でもメンテナンス回数が少なく環境にも貢献できます。 - 高い安全性
外部からの圧力などによって内部短絡が発生する状況においても、発煙・発火の可能性が極めて少なく
自動車、産業機器、定置用など高い安全性と信頼性が要求される様々な分野での使用が可能です。 - 急速充電
6分間で80%以上*の充電が可能であり、自動車やバス等も急速充電が可能です。
また、急速充電を繰り返しても、劣化が少なく安心して使用できます。 - 高入出力
大電流での充放電が可能なため、鉄道や自動車の減速時に発生する大きな回生電力を蓄電したり、モータの始動に必要な大電流を供給することが可能です。 - 広い動作温度範囲
低温で充電しても金属リチウムが析出しないため、-30℃*の低温環境下で繰り返し充電・放電が可能です。
-
広い実効SOCレンジ
SOC**の広い範囲に亘って高い入出力特性を持つため、SOC0~100%で使用可能です。システムの電池搭載量の削減が可能です。
*セルの種類や使用条件により特性は異なります
** SOC:State of Charge:充電状態
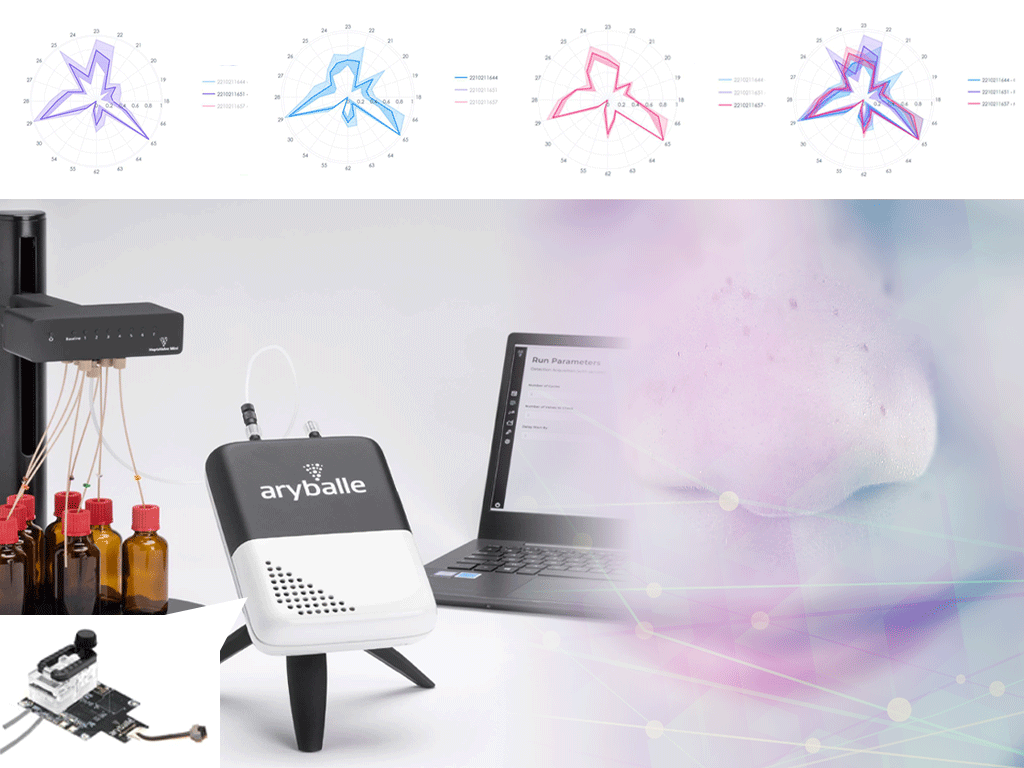
- 製品紹介
新方式においセンサーとは?
- 人間の嗅覚のようににおいの種類を検出・識別してデータ化できる
- リアルタイムで測定ができる
- 特許技術のシリコンフォトニクス式は異なるにおいを連続して測定が可能
従来のにおい測定の難しさ
においは人によって感じ方が違ったり、同じにおいを嗅ぎ続けると感覚が鈍ってしまいます。
また同じ人でもその日の体調や温湿度などの環境変化によっても感じ方が変わります。
人が一定の条件で測定することが難しい曖昧な要素です。
シリコンフォトニクス式においセンサーの特徴
においの元となる有機性揮発化合物(VOC)がバイオセンサーに付着することでバイオセンサーが反応します。
その反応をレーザーと光学センサーで捉え、においのパターンをサーバーに送信して表示・分析をすることでデジタル嗅覚として使用できます。
バイオセンサーはVOCが付着しやすく剥がれやすい特徴を持っているので、短時間で異なるにおいを計測できます。
においセンサーの活用例
- 食料品や化粧品などの製造工程では製造ロットによる品質のバラつき検知
- 原材料の品質チェック
- 新製品開発の際にかおりの時間経過による変化の観察や条件をかえたサンプルの分析
- 従来は感覚でしか表せなかったにおいについてデータを根拠にしたレポートの作成

圧着コネクタとの比較で見えたスリーエムジャパンの『ミニクランプⅢ』が製造現場を変える理由とは?
- 製品紹介
『ミニクランプⅢ』のポイント
- 4芯の結線作業がわずか14秒で完了する、専用工具がいらない画期的なセンサー用圧接コネクタ。
- 加工時間を大幅に短縮し、製造コストの削減に貢献!初心者でも簡単に使える設計。
製品の特徴
ミニクランプⅢの最大の特徴は、電線の被覆を剥く必要がない圧接方式を採用していることです。
結線に必要な時間を驚くほど短縮できます。
また、特殊な工具を必要とせず、誰でも簡単に扱える設計です。
- 4芯圧着コネクタと比較すると結線作業にかかる時間を80%以上削減可能
- 工具が不要なので作業に慣れていない人でも簡単導入
- センサー用に最適化された高い接続品質
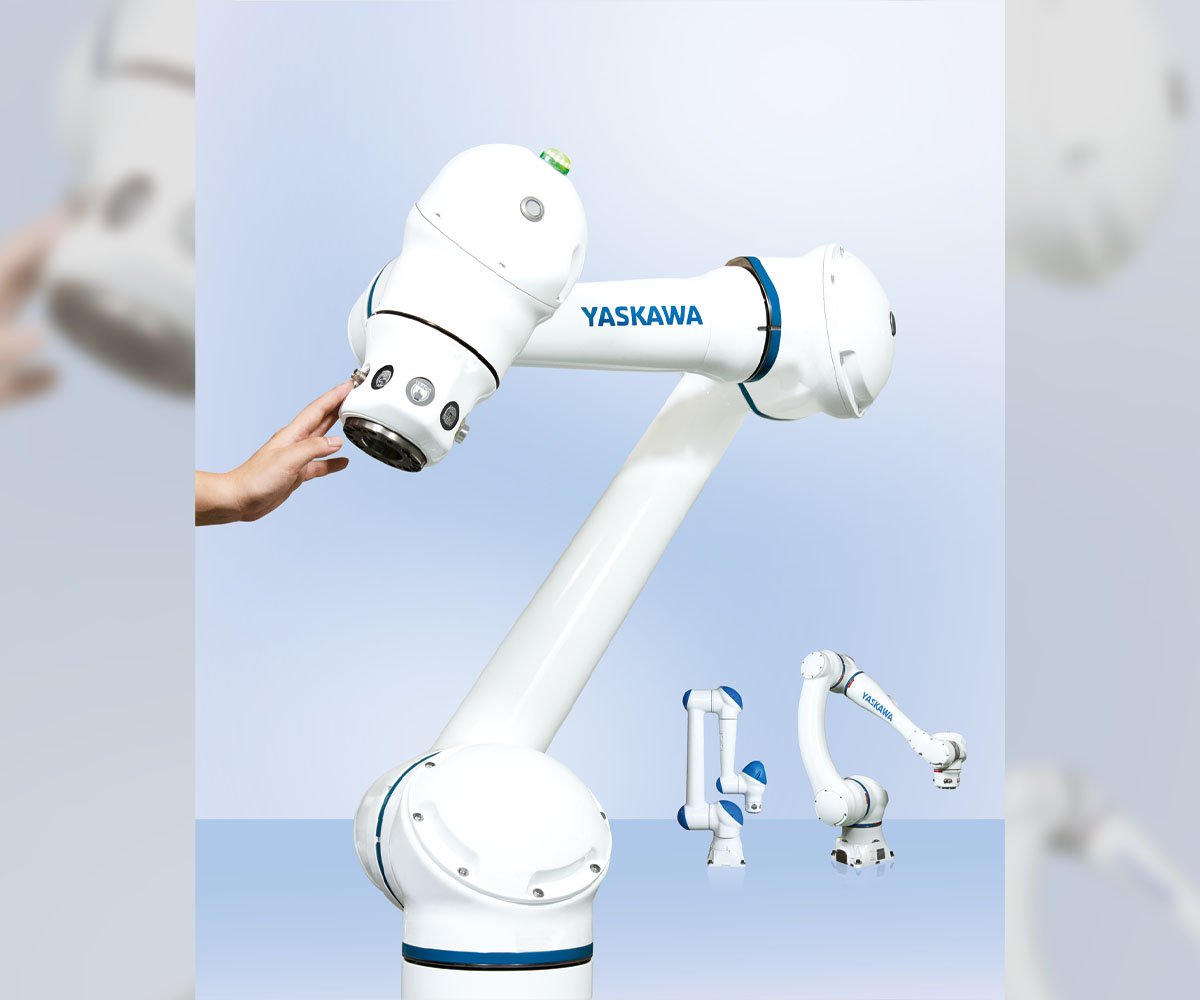
- 製品紹介
「産業用ロボット」とは違って、安全柵がなくても作業員がいるスペースで安全に協働できるよう設計されている「人協働ロボット」。作業員の仕事を分担し、補助する「人協働ロボット」は、作業員の安全確保や人手不足の解消など、製造現場の様々な課題解決や品質向上に価値を発揮する機器です。この記事では、サンワテクノスの取り扱い製品である安川電機製の「人協働ロボット MOTOMAN-HCシリーズ」について、その特徴をご紹介します。
安全柵は必要なし!限られたスペースでも設置可能。
安全柵の設置義務があり、導入するには広いスペースの確保が必要な「産業用ロボット」に比べて、「人協働ロボット MOTOMAN-HCシリーズ」は、既存の作業環境での導入が可能です。その理由は、ロボットに搭載されている安全機能。「産業用ロボット」のように安全柵を設置することも、広いスペースの確保も不要で、導入しやすいというメリットがあります。
※「人協働ロボット MOTOMAN-HCシリーズ」は産業用ロボットのための安全要求事項を定める国際規格「ISO10218-1(日本産業規格ではJIS B 8433-1に該当)」に準拠しています。また、ロボットコントローラの「安全機能」は,国際規格「ISO 13849-1PLd(Cat.3)」に適合しており、第三者認証機関より安全認証を取得しています。これらの安全機能により、HCシリーズは安全柵なしのシステム構築が可能ですが、全てのケースにおいてお客さまにてリスクアセスメントを実施する必要があります。
怪我や事故を防ぐ、人にやさしい安全設計。
「人協働ロボット MOTOMAN-HCシリーズ」は、作業員の近くで作動させることを前提とした安全設計。人や物に触れるとすぐに安全に停止したり、一定のスピード以下に動きをコントロールしたり、ロボットに物が挟まれても取り出せるように自動で動いたりと、怪我や事故を引き起こさないための機能が充実しています。ロボットの構造や形状そのものも、安全性にもとづく設計で、作業員の安全を確保します。
※ISO20318-1/ISO13849-1第3者認証取得
初心者でも操作かんたん。タブレット感覚で教示できる。
専門のエンジニアがいないから、導入が難しい。ロボットの扱いに慣れていないから、うまく操作できるか不安。「人協働ロボット MOTOMAN-HCシリーズ」なら、そうした心配は無用です。従来の「産業用ロボット」は、専門のエンジニアによるティーチングが必要なのに比べて、「人協働ロボット MOTOMAN-HCシリーズ」はロボット操作に慣れていない人でも、およそ30分でピックアンドプレイス動作のティーチングが習得できます。それを可能にしているのが、タブレット感覚で操作できるスマートペンダント。直感的にロボットを操作できるように工夫されており、専門的なエンジニアが不在でも、安心してロボットを導入・活用できます。
使用用途に合わせた豊富なラインナップ。
「人協働ロボット MOTOMAN-HCシリーズ」は、多様な仕様の製品を取りそろえています。水・切削油などの液体や、切りくずなどの粉じんにさらされる環境においても使用できる防じん・防滴仕様や食品仕様。大型ワークの搬送や複数ワークの搬送作業にも適用可能な高可搬タイプ。豊富なラインナップで、多様な作業環境のものづくりをアシストします。
豊富なネットワークを強みに、工場の課題解決に貢献するサンワテクノス。
作業員の安全を確保しながら、従来の作業環境に導入可能な「人協働ロボット MOTOMAN-HCシリーズ」。人手不足の解消や工場の自動化など、課題解決をサポートする技術や機能が搭載されており、ものづくりをよりスマートに後押しします。サンワテクノスでは、株式会社安川電機と連携しながら、製造現場における課題やご要望のヒアリング、技術的なご提案、導入にいたるまで一貫した技術支援を行っております。「人協働ロボット MOTOMAN-HCシリーズ」についてご興味のある企業様は、ぜひお気軽にお問合せくださいませ。
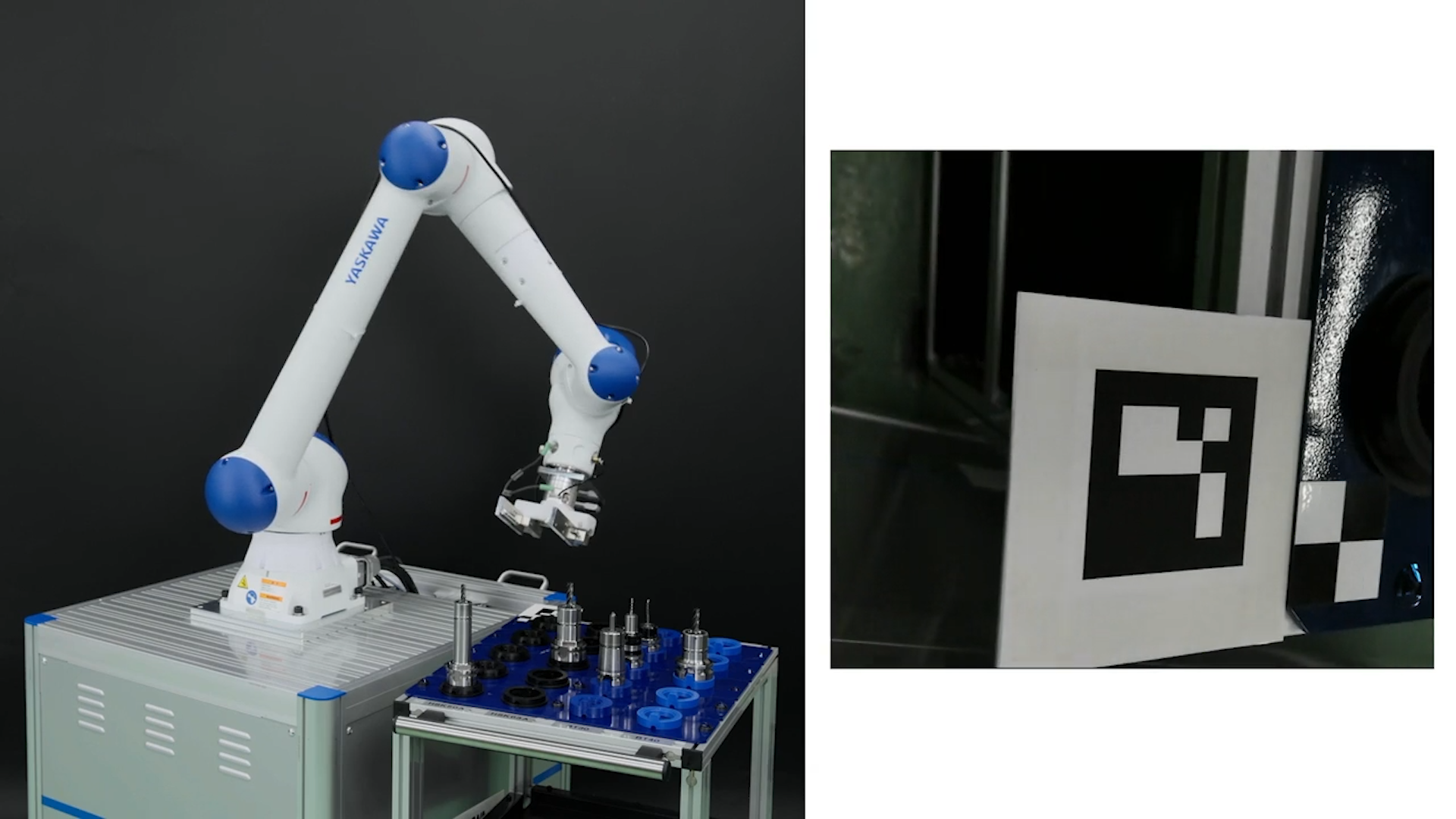
- 製品紹介
労働力不足への対応や、生産性の高い多品種変量生産の実現。ものづくりにおける課題を解決し、品質向上を達成するにはデジタルマニュファクチャリングの推進が欠かせません。サンワテクノスは株式会社エムテックとの協働で、仮想空間を活用したデジタルマニュファクチャリングを実現するロボットソリューションパッケージ「3D Connect シリーズ」を開発・発売しています。この記事では、その第一弾目の製品であるAR マーカーを利用したロボットソリューションパッケージ「AR^2 System(エーアール・ツー・システム)」についてご紹介します。
「3D Connect シリーズ」は、三次元CADとロボットなどのモーションコントローラーをリアルタイムに連携操作させるプロセスシミュレーター「Planning Simulator」を用いて、設計から動作に至る各種機能を持ったモジュールを組み合わせたソリューションパッケージです。 これにより、ロボット動作における現実と仮想空間の座標の齟齬が補正され、ものづくりにおけるデジタルマニュファクチャリングが促進されます。
標準的なロボットは、ロボット座標で管理を行うため、対象物との相対位置がずれると再度ティーチングを行う必要があります。「AR^2 System」では、ロボットに搭載したカメラが AR マーカーを読み取り、自動座標定位を行うことで高精度にロボットの相対的位置を補正。ロボットが移動しても、ARマーカーからの相対距離で作業を行います。そのため正確な位置決めが不要になり、必要な場合にのみロボットを設置して作業させたり、移動して作業をさせたりすることも、AR マーカーを用いることで容易に可能となります。
「AR^2 System」の機能拡充とさらなる利便性の向上を目指し、オプションで追加できる機能を開発中です。同一のカメラを利用してパターンマッチングなどの画像処理を行ったり、コンベヤトラッキングなどの機能を追加したりと、一つのカメラで複数の機能を果たします。これは位置認識のみを行う既存製品との大きな違いです。
システムの立ち上げは、パソコンにロボットコントローラーとカメラを接続すれば準備完了。初期設定もウィザードに従うだけで簡単にできます。これまでロボット導入にハードルを感じていた企業様にとっても、容易に導入が可能です。
ロボット導入へのハードルを下げ、生産性向上に貢献する「AR^2 System」。単に自動化するためだけのロボットではなく、ロボット自身が自由に移動し、ワーク自体が移動した時点でもロボットとの相対関係を認識して補正できるアプリケーションで、製造現場の高度なニーズに応えます。サンワテクノスでは、株式会社エムテックと連携しながら、製造現場における課題やご要望のヒアリング、技術的なご提案、導入にいたるまで一貫した技術支援を行っております。ご興味のある企業様は、ぜひお気軽にお問合せくださいませ。
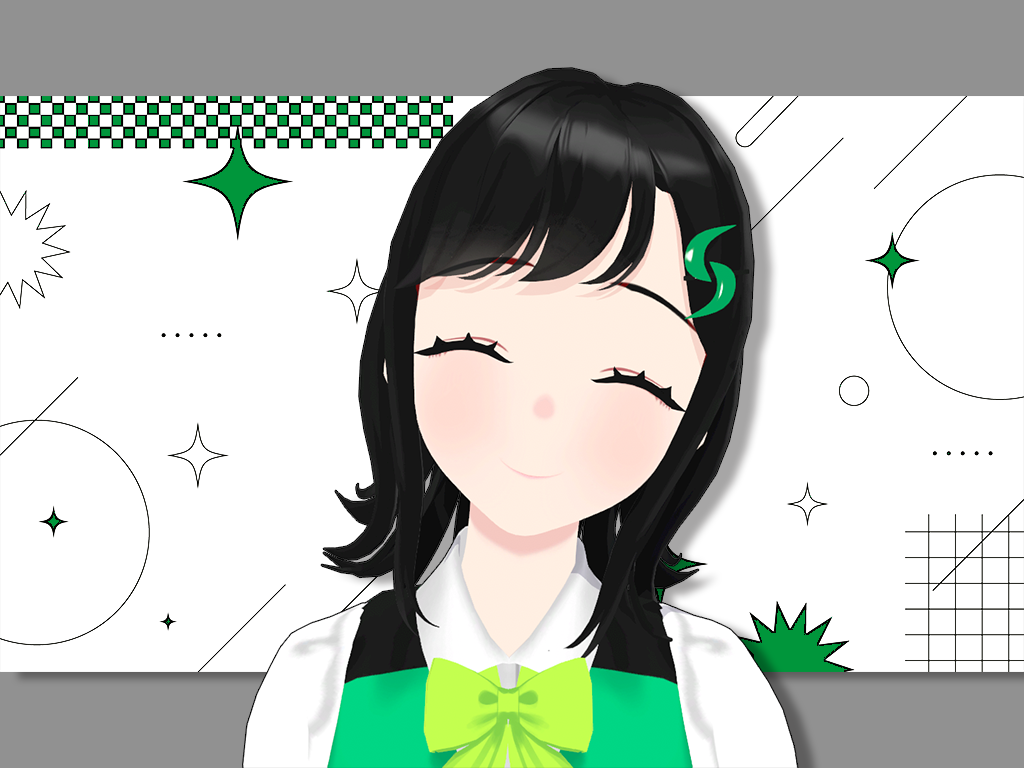
- お役立ち情報
プロフィール
お世話になっておりますサンワテクノスの三來部さんわ(みくるべさんわ)です!
まずは私について簡単にご紹介します!
- 肩書:バーチャルプロモーション担当
- 趣味:動画の制作(企画から編集まで全般やってます!)
- 座右の銘:「分かりやすく面白く!」
- 好きなこと:みなさんからの質問や感想を聞くこと。おしゃべりも大好きです♪
わたしのお仕事は?
- 主に公式YouTubeチャンネル「さんわちゃんのお仕事応援チャンネル」の運営をしています!
このチャンネルでは、製品やサービスの魅力をしっかりお届けするために、以下のような動画をお届けしています。 - 製品・サービス紹介
新しい製品やサービスの使い方や特徴について、楽しく解説します!
おなじみの製品から専門性の高いニッチなものまで、分かりやすく楽しい動画を配信しています♪ - 課題解決サポート
「こういう問題を解決したい」「こういうことで困っている」そんな課題を解決するための動画も制作しています。
御社の課題も解決できるかも! - インタビュー
製造業の企業さんにお邪魔して、ものづくりに携わっている方々に直接インタビューを行っています。
製品が生まれていく工程や、現場で行われている工夫についてお届けします!
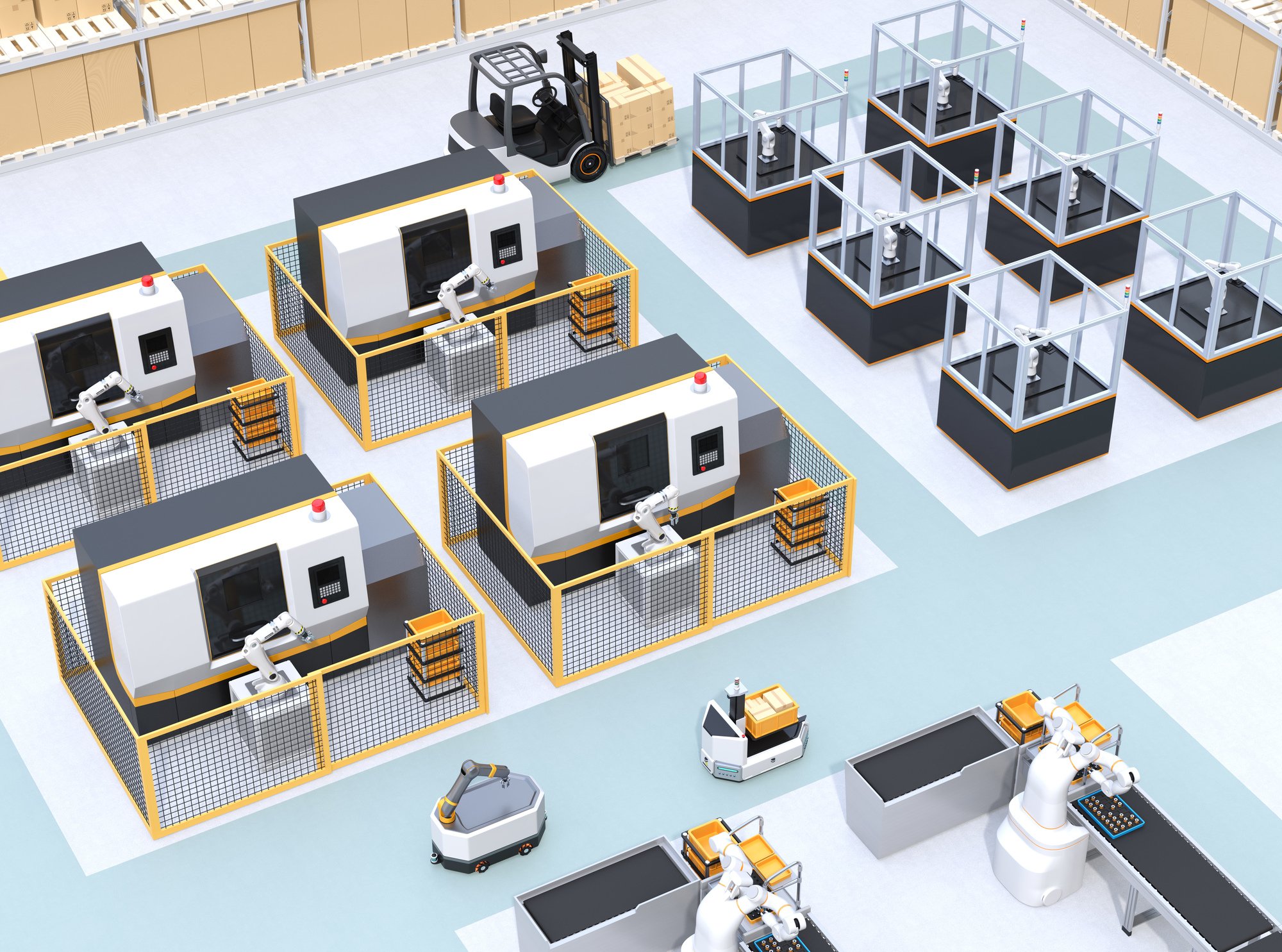
- お役立ち情報
「産業用ロボット」を導入する企業に義務付けられている「安全対策」。「労働安全衛生法」や「ISO 10218」といった法令・規定が定められており、企業はこうした法的な安全措置をとることで、作業員の安全確保や事故防止に努める必要があります。この記事では、法令や規格について述べながら、安全対策の手順や注意事項、具体的な対策例についてもご紹介します。
「産業用ロボット」の安全対策に関する基準
「産業用ロボット」の安全対策に関わる法令や規格には、「労働安全衛生法」と「ISO10218」があります。
(1)労働安全衛生法
「労働安全衛生法」では、「産業用ロボット」の設置と運用についての具体的な安全基準が定められており、安全柵の設置が義務付けられています。
“”「産業用ロボット(定格出力が80Wを超えるもの)」に接触することにより危険が生ずるおそれがあるときは、さく又は囲い等を設けること“”(労働安全衛生規則第150条の4)
安全柵は、ロボットと人の接触や事故などを未然に防ぐためのものです。ただし、リスクアセスメントを行い、作業者の安全確保が証明できれば、設置義務が免除される場合があります。例えば、センサーが取り付けられたライトカーテンや、セーフティレーザースキャナの設置など。具体的な安全対策については、記事の後半でご紹介しています。
(2)ISO 10218
「ISO 10218」は、「産業用ロボット」の安全基準について「国際標準化機構(ISO)」によって定められた規格です。ロボットの設計や製造、設置、運用について細かに規定されています。「ISO10218」を遵守することで国際的な安全基準をクリアでき、ビジネスをグローバルに広げていくアドバンテージとなります。
考えられるリスク
産業用ロボットの運用においては、以下のような具体的なリスクが考えられます。
(1)自動運転中の作業者の侵入
ロボットの可動範囲に作業者が誤って侵入することで、大けがを負う可能性があります。このリスクを低減するためには、センサーを設置し、作業者が侵入した場合にロボットが停止するようにする必要があります。
安全対策・リスクアセスメントを行う際の注意点
産業用ロボットの安全対策やリスクアセスメントを実施する際には、以下の注意点に留意することが重要です。
(1)危険源の特定
産業用ロボットのリスクアセスメントでは、まず危険源を特定することが重要です。新たに機械を新設・改造する際に、潜在的な危険源を洗い出し、それがどのような危害をもたらすかを評価します。
(2)リスク評価の正確性
リスク評価は、危害の発生確率とその影響の程度を正確に評価することが求められます。評価が不十分だと、重大なリスクが見逃される可能性があります。
(3)適切なリスク低減策の実施
特定されたリスクに対しては、本質安全対策や安全防護対策を講じる必要があります。具体的には、セーフティセンサーの設置や安全柵の設置などが挙げられます。
(4)作業手順書と教育の見直し
リスクアセスメントの結果に基づいて、作業手順書の見直しや社員への教育を行い、リスク低減策が確実に実施されるようにします。
(5)フィードバックと継続的な改善
実際の運用中に新たなリスクが発見された場合、フィードバックを基にリスクアセスメントを再度実施し、継続的に改善を図ることが重要です。
(6)法規制の遵守
リスクアセスメントは、労働安全衛生法やISO規格などの法規制に基づいて実施する必要があります。これにより、法的要求事項を満たし、安全性を確保します。
(7)メンテナンス時の安全確保
ロボットのメンテナンス時には、可動部の接触などのリスクがあるため、安全ハーネスの使用や作業手順の見直しが必要です。
これらの注意点を踏まえて、産業用ロボットのリスクアセスメントを徹底することで、労働者の安全を確保し、けがや事故を未然に防ぐことができます。
「産業用ロボット」の安全対策の例
ここからは、具体的な安全対策の事例をご紹介します。
(1)安全柵の設置
「産業用ロボット」を導入するにあたり、最も普及している安全対策です。ロボットのまわりに柵や囲いを設置し、人とロボットを隔離します。安全柵の設置には、以下のようなポイントがあります。
○ 法令遵守:労働安全衛生法および労働安全衛生規則に準拠した設置が必要です。特に、定格出力が80Wを超える産業用ロボットで、接触により危険が生じるおそれがある場合は、柵または囲いの設置が義務付けられています。
○ リスクアセスメントの実施:安全柵の設置前に、作業環境や作業内容に基づいたリスクアセスメントを行い、適切な安全対策を選択することが重要です。
○ 人とロボットの作業エリアの明確な分離:安全柵は、人の作業場所とロボットの可動範囲を明確に分離するように設置する必要があります。
○適切な材質の選択:例えば、食品工場などでは衛生面を考慮し、ステンレス製の安全柵を選択するなど、作業環境に適した材質を選ぶことが重要です。
○ メンテナンス性の考慮:定期的な点検や清掃が容易に行えるよう、アクセスしやすい構造の安全柵を選択することが望ましいです。
○国際安全規格への適合:EN ISO12100、EN ISO13857、EN ISO10218-2などの国際安全規格に適合した安全柵を選択することが推奨されます。
○作業効率への配慮:安全柵の設置が他の作業に支障をきたさないよう、設置スペースや作業動線を考慮する必要があります。
○ 補完的な安全装置の併用:必要に応じて、ライトカーテンやセーフティレーザスキャナなどの安全装置を併用し、より高度な安全性を確保することも検討すべきです。
これらのポイントを考慮しながら、作業環境や作業内容に応じた適切な安全柵の設置を行うことが重要です。また、安全柵の設置後も定期的な点検とメンテナンスを行い、常に安全性を維持することが求められます。
(2)ライトカーテン
安全柵により安全性が確保されていても、人が立ち入るための開口部やドアが設置されている場合には、ライトカーテンやドアスイッチが、侵入を検知する設備として用いられます。
こうした対策を講じていても、安全柵の内側に人がいる時にロボットが作動し、怪我や事故が発生するリスクも考えられます。特に事故要因として挙げられるのが、設備の死角。設備が大きくなるほど死角が増え、そこに人がいるのに気づかないままロボットを起動してしまうというものです。これを防ぐために、「起動および再起動」時の安全性について、「ISO10218-2」ではこのように規定されています。
○起動及び再起動の制御機器は、安全防護空間外に配置し、手動で操作されなければならない
○オペレータは、各制御位置から、安全防護空間内に誰もいないことが確実に確認できなければならない
○これが現実的でない場合には、安全防護空間のいたる所にオペレータを検知するための存在検知を備えなければならない
つまり、安全性を確保するためには、設備の死角に人がいないかどうかを検知した上で、ロボットを起動させる必要があります。この解決手段として、「レーザースキャナ」が挙げられます。
(3)セーフティレーザースキャナ
前述した安全性確保においても、安全柵を設置せずに対策を講じる場面でも、人の存在を検知するための機器が必要です。その一つが、「セーフティレーザースキャナ」です。最新の「セーフティレーザースキャナ」は、従来の製品に比べて検知する領域が広くなったり、誤検知などの作動不良が改良されたりと、実用性の高い製品が誕生しています。
豊富なネットワークを強みに、工場の課題解決に貢献するサンワテクノス。
「産業用ロボット」を導入している企業にとって、「労働安全衛生法」や「ISO10218」で定められている安全対策の遵守は義務です。安全性を確保しながらも、生産性の向上や品質の安定をはかることで、さらなる事業拡大が期待できるでしょう。サンワテクノスでは、メーカーと連携しながら、製造現場における課題やご要望のヒアリング、技術的なご提案、導入にいたるまで一貫した技術支援を行っております。「産業用ロボット」の安全対策についてご検討されている企業様は、ぜひお気軽にお問合せくださいませ。
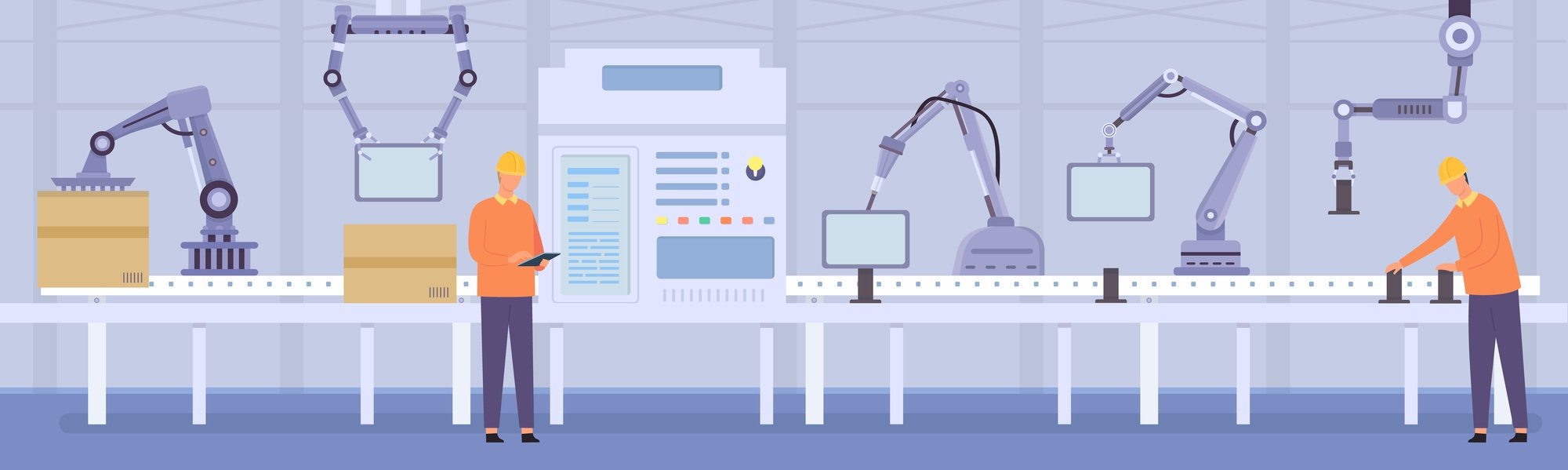
- お役立ち情報
人件費削減や人手不足の解消、安全の確保や作業における柔軟性といった観点から、工場の様々なニーズに応える存在として、多くの製造現場で導入が進められている「協働ロボット」。この記事では、「産業用ロボット」との違いや「協働ロボット」導入にあたってのメリット・デメリット、必要となるコストや導入手順などについてご紹介します。
協働ロボットとは
協働ロボットは、人間と協力して作業を行うように設計されたロボットです。これらのロボットは、安全機能が組み込まれており、人間と同じ空間で作業することが可能です。協働ロボットは、製造業や物流業、医療分野などで使用され、人間の作業を補完し、生産性を向上させることを目的としています。特徴としては、柔軟性、安全性、簡単なプログラミングなどが挙げられます。
【メリット】省スペースで、人との分業が可能。誰でも扱いやすい。
協働ロボットには様々な導入メリットが挙げられます。
(1)人との協働作業が可能
協働ロボットは、人と同じ作業スペースで安全に作業できるため、生産ラインに並んで単純作業や反復作業を行うことができます。これにより、人とロボットの効率的な分業が可能になります。
(2)柔軟な運用
協働ロボットは移動が容易で、日替わりで作業内容や場所を変更できます。これにより、タクトタイムの超過している作業部分に柔軟に対応できます。
(3)安全柵いらず
安全柵を設置し、作業員との距離を確保する必要がある「産業用ロボット」とは違い、「協業ロボット」は人の安全を考慮した設計となっているため安全柵を設置する必要がありません。そのため、限られたスペースであってもロボットを設置できたり、移動させたりすることも可能です。また、協働ロボットは人がいる空間での作業に用いられるため、特定の製品の製造にのみ使用したり(もしくは使用しない)、作業員と分担して作業を行うことにより、設備費のイニシャルコストが削減できる可能性もあります。こうしたメリットから、特に小ロット・多品種の製造現場などにおいて、協働ロボットは実用的な機器だといえるでしょう。
(4)専門のエンジニアがいなくてもOK
専門のエンジニアがいないから、ロボットの導入にハードルを感じている。そんな企業様も少なくないでしょう。協働ロボットは、ロボット操作に不慣れな人でも直感的に操作しやすいように、機能面の開発も進んでいます。具体的には、ロボットに動作を教える「ティーチング」が専門のエンジニアではない人でもできるようになっていたり、「ハンドユニット」さえあれば、専門業者を呼ばなくても自社でロボットの動作をカスタマイズできるようになっていたり。このように協働ロボットは、特定の技術者だけが扱えるロボットではなく、「誰でも扱いやすい」ロボット。協働ロボットを導入することにより、活用アイデアが生まれたり、生産性の向上が期待できたりと、製造を加速させる起点になるといえます。
【デメリット】協働ロボットの特性による対応力の限界。
「協働ロボット」はメリットだけでなく、デメリットもあります。
(1)動きが遅い
協働ロボットは、人がいる空間で作業し、人に接触しても安全に停止することを前提に設計されているため、「産業用ロボット」よりも動くスピードが一定以下に設定されています。しかし製品によっては、“協働モード”と“産業用ロボットモード”の切り替え機能付きの協働ロボットも開発されており、場面や用途によって使い分けも可能です。センサーと連動し、人が近くにいない場合は“産業用ロボットモード”でスピーディに動作し、人が近くにいたら“協働モード”で安全性を優先する。こうした使い分けにより、安全性を確保しながら作業効率を高めることができます。
(2)パワーに限界がある
協働ロボットの可搬重量は製品によって様々ですが、500g~30kgのものが多く、産業用ロボットに比べるとパワー不足が懸念されます。しかし捉え方を変えれば、これまで作業員が行っていたピッキングや部品の取り付けなど、パワーが必要のない作業については、協働ロボットで代用可能です。近年は30kgの可搬タイプも市場に出回りはじめ、パレタイズ作業にも協働ロボットを活用している事例もあります。
(3)高価格
安全性の確保や、専門性がなくても作業できる使い勝手の良さなど、様々なメリットがありつつも、協働ロボットの普及率は産業用ロボットに比べて低いのが現状です。各軸に力学センサーを内蔵していることから製品が高価格であることも、その一因にあると考えられます。しかし、今後のロボット開発の進歩により、製品のコストダウンや普及率の向上も十分に見込めるでしょう。
協働ロボットの導入ステップ
協働ロボットの導入にあたり、以下の手順を踏むことで導入が円滑に進みます。
(1)潜在的ニーズの発掘と課題の明確化
現状の作業工程を見直し、潜在的なニーズを発掘します。そして、解決すべき具体的な課題を明確にします。
(2)導入目的の設定
課題に基づいて、協働ロボット導入の具体的な目的を設定します。例えば生産性向上、品質改善、作業員の負担軽減などが該当します。
(3)適切なロボットの選定
業務別のニーズに合ったロボットを選定します。作業内容や目的に応じて、ロボット本体やアームの動かし方などを検討します。
(4)システム設計
ロボット設計、安全設計、周辺設計、制御・センシング設計を行います。これには生産ラインの構築や安全規格に沿った設計も含まれます。
(5)リスクアセスメントと安全対策
ロボット導入により発生するリスクを解析し、必要な安全対策を講じます。
(6)プロジェクト・マネージメント
計画段階から運用開始まで、プロジェクト全体を管理します。
(7)導入とテスト
設計に基づいてロボットを導入し、実際の運用環境でテストを行います。
(8)教育・トレーニング
ロボットを操作する作業員に対して、必要な教育やトレーニングを実施します。
(9)運用開始と評価
実際の運用を開始し、導入目的が達成されているか評価します。
これらのステップを適切に実行することで、協働ロボットの効果的な導入が可能になります。また、初めての導入や専門知識が不足している場合は、ロボットシステムインテグレータ(SIer)のサポートを受けることも有効です。
協働ロボットの導入に必要なコスト
協働ロボットの導入には、本体価格以外にもさまざまなコストがかかります。主に、以下の費用が挙げられます。
(1)協働ロボット本体
一般的に200万円〜500万円程度です。ただし、最近では100万円台の低コストモデルも登場しています。
(2)周辺機器
○グリッパーやセンサーなどのロボットに直接取り付ける装置
○ロボット架台
○ベルトコンベアや加工機などの生産ライン構築に必要な設備
○PLC (プログラマブルロジックコントローラ)
(3)システムインテグレーション (SIer) 費用
ロボットの導入から稼働までをサポートするSIer会社への支払いです。コンサルティング、設計、周辺機器の手配、システムの組み立て、ティーチングなどが含まれます。
(4)人材教育・育成費用
ロボットの操作やメンテナンスを行う担当者の教育にかかる費用。
(5) 安全対策費用
リスクアセスメントや安全装置の導入にかかる費用。
具体的な総コストは、導入する環境や目的によって大きく異なりますが、ロボット本体価格の数倍以上になることが多いとされています。協働ロボット導入の費用対効果は、単純な費用だけでなく、生産性・品質向上などの直接的メリットや、人材採用・教育コスト削減、離職リスク回避などの間接的メリットも含めて、広い視野で検討することが重要です。
豊富なネットワークを強みに、工場の課題解決に貢献するサンワテクノス。
人手不足の解消や安全性の確保、生産性向上など、製造現場をとりまく様々な課題やテーマに対して価値を発揮する「協働ロボット」。サンワテクノスでは、メーカーと連携しながら、製造現場における課題やご要望のヒアリング、技術的なご提案、導入にいたるまで一貫した技術支援を行っております。「協働ロボット」の導入をご検討されている企業様は、ぜひお気軽にお問合せくださいませ。